Monitoring Information By Industry - Printing and Publishing
On this page:
- The Printing Industry
- Major Types of Printing Processes
- Major Emissions Sources and Pollutants
- Air Pollution Control Techniques
- Monitoring Information
- Permits
- Applicable Standard Industry Classifications Codes
- Applicable Source Classification Codes
- Applicable NAICS Codes
- Regulations
- Related Industry Regulations
The Printing Industry
It is estimated that 97 percent of all printing activities can be categorized within five different printing processes: lithography, gravure, flexography, letterpress, and screen printing. The equipment, applications, and chemicals for each of these processes differ; however, they all print an image on a substrate following the same basic sequence. The fundamental steps in printing are referred to as imaging, pre-press, printing, and post-press operations. The type of printing process used depends on a variety of factors, including the substrate (e.g., paper, plastic, metal, ceramic, etc.), the length and speed of the print run, the required print image quality, and the end product.
The first step in the printing process, imaging, produces an image of the material to be printed. Traditionally, this image is produced photographically, but with increasing frequency the image is produced electronically. The production of a photographic image involves a variety of chemicals similar to those used in other fields of photography. The image on the film is transferred to the image carrier or plate. In pre-press operations, an image carrier is produced that can transfer the ink in the image area and can repel the ink in non-image areas. In printing, ink is applied to the plate and the image is transferred to the substrate. In the post-press step, the printed material may receive any one of numerous finishing operations, depending on the desired form of the final product.
The emissions from the industry are primarily Volatile Organic Compounds (VOC) and organic Hazardous Air Pollutants (HAP). The emissions result from evaporation of VOC and HAP contained in the inks during the printing process.
For a more detailed description of the printing and publishing technologies select one of the following links.
Major Types of Printing Processes
In general, the imaging and post-press operations are fairly similar for all printing technologies. Imaging operations begin with composition and typesetting and are followed by the production of a photographic negative or positive. Once the desired format and images are assembled, they are photographed to produce transparencies. The printing industry photographic process uses input materials very similar to those used in other fields of photography. The purpose of this step is to produce a photographic negative (for lithography and letterpress) or a positive (for gravure, screen printing, and other lithographic processes).
From a photographic negative or positive, a plate is produced that is used in each printing process to carry or transfer ink in the form of the image to the substrate. The plate must pick up ink only in the areas where ink is to be applied to the final image on the substrate. Each of the five predominant printing technologies differs significantly in how the image is transferred from the image carrier to the substrate in the printing step. Each of the technologies employs different types of plates. Each of the printing technologies is briefly discussed in the following sections.
Offset Lithography
Offset lithography is the most common form of commercial printing. It relies on the fact that water and oil do not mix. A lithographic printing plate has non-image areas that absorb water. During printing, the plate is kept wet with water, which is absorbed by the non-image areas. The ink, which is inherently greasy, is rejected by the areas wetted by water and instead adheres to the image areas.
In offset lithography, both water and ink are transferred to the plate cylinder, which holds the plate of the image to be printed. This image is transferred to a blanket cylinder and then to the paper that is being printed. Printing by the blanket cylinder, rather than directly printing from the plate cylinder, is the reason for the term "offset". Use of the rubber-surfaced blanket cylinder protects the delicate plate and allows textured papers to be easily printed.
Flexography
Flexography is a form of printing in which raised surfaces on a flexible plastic or rubber plate come into contact with, and transfer ink to, the substrate (the surface being printed). Over 90 percent of flexographic applications are in the packaging and specialty products industries. Flexography is particularly suited for printing flexible packaging such as plastic wrappers, labels, foil, and paper products. Flexographic presses may be a relatively small part of the overall manufacturing process at packaging facilities, especially those that produce flexible packaging.
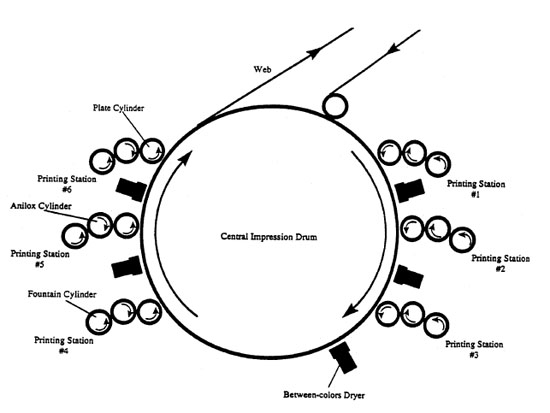
Although there are a variety of different flexographic printing presses, three general types are used in the packaging industry: central impression (CI), stack, and in-line. Each of these presses is distinguished by the number of impression cylinders used and the arrangement of the printing stations (printing cylinders). On a CI press, the printing stations are arranged around one common impression cylinder (see links below for figure). In contrast, each printing station on a stack or in-line press has its own impression cylinder. On a stack press, sets of printing stations are arranged vertically; on an in-line press, the stations are arranged horizontally (see links below for figure).
Flexography is also used to print many publications, although this industry is much smaller in size than the flexographic packaging industry. Some publications, including newspapers, phone directories, and catalogs, are printed with water-based inks (rather than solvent based inks). Dedicated flexographic presses exist for newspaper and commercial printing.
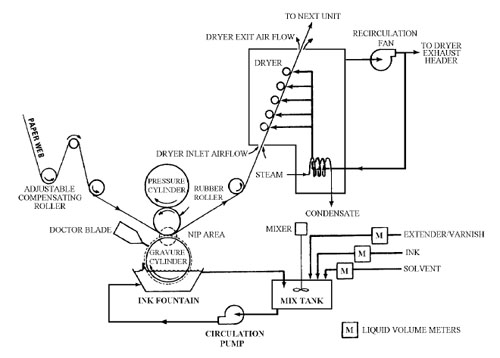
Publication Rotogravure and Product Rotogravure
Rotogravure printing is a form of printing in which ink is transferred to the substrate from small, recessed cells engraved in the surface of a cylinder. Almost all rotogravure printing is done on webbed substrate. Rotogravure presses have printing stations that are connected in-line with each other. As with in-line flexographic printing, each rotogravure station has its own impression cylinder. Although only four printing stations are required to print each side of the web, publication rotogravure presses in the United States can have up to 16 stations. As with flexographic packaging processes, publication and product rotogravure are typically a relatively small part of the overall manufacturing process.
Letterpress Printing
Letterpress printing is one of the oldest forms of printing. In its most basic form, it involves pressing inked blocks onto paper. Raised images and type, on blocks of metal, wood, or linoleum, are locked in place and covered with ink by a roller (also called a dauber). The ink-covered blocks are then pressed onto paper, producing the printed images and type. Since the images and type that are covered with ink are raised, letterpress printing is a form of relief printing.
Screen Printing
Screen printing involves using a squeegee to force ink or dye through a porous screen mesh. An image is formed because the stencil, which is added to the screen, blocks out certain areas on the mesh.
Screen printing of textiles may be performed with either flat-bed or rotary screen presses. Flat bed screen presses are used to print on garments or fabric pieces. Flat bed presses may be either manual or automatic (automatic movement from one color station to the next). Automatic presses also typically have automatic operation of both the squeegee and flood bar (which redistributes ink on the screen, after the squeegee has been used). Rotary screen presses use metal cylindrical screens to print on rolls of fabric.
Coating thicknesses in screen printing are typically much thicker than in other forms of printing. In screen printing coating thicknesses range from 20-300 microns, whereas coating thicknesses in other forms of printing range from 1 micron (offset lithography) to 6 microns (ultraviolet flexography).
Post-Press Operations
Post-press operations at printing facilities may include one or more binding and/or finishing steps. These steps include, but are not limited to, cutting, folding, trimming, die cutting, embossing, foil stamping, drilling, saddle stitching, sewing, perfect binding, vacuum forming, and gluing. The gluing steps range from the application of a hot melt adhesive to the back of a book or magazine, to laying of a laminate to the printed substrate. Adhesives used fall into three broad categories: hot melts, water-based, and solvent-based. Most hot melt and water-based adhesives have little or no VOC content.
Major Emissions Sources and Pollutants
Emissions from printing operations result primarily from evaporation of organic solvents contained in the inks. Most of the solvent contained in the ink evaporates during the process, although some solvent may remain with the printed product leaving the facility. The organic solvents used in the ink may be Volatile Organic Compounds (VOC) or Hazardous Air Pollutants (HAP). Some inks may be water-based and do not produce emissions.
In general, the emissions points from a printing line (operation) include the: 1) ink fountain, 2) the press, 3) the drier, and 4) the chill rolls [actual emissions points vary by the type of printing operation]. Typically, a large fraction of the emissions are associated with exhausts from ink in the drying units (drier). Driers typically use natural gas or electricity to heat air. The warmed air passes over the substrate in the drier, causing the volatile compounds in the ink on the substrate to evaporate. The drier exhaust air containing the volatilized solvents is contained in a duct and the air stream is vented to the atmosphere; the air stream may be directed to an air pollution control device (APCD) prior to venting to the atmosphere.
Emissions that are not collected and routed to a duct or stack are called fugitive emissions. Fugitive emissions can come from several sources in a printing operation, such as ink feeding systems and the chill rolls. Vapor capture systems (e.g., ventilation hoods, floor sweeps, or enclosures) may be used to capture, contain, and exhaust the emissions from these sources (to an air pollution control device), thereby reducing the amount of fugitive emissions. The printing equipment may include vapor capture systems as part of the design and operation of the equipment.
Other sources of fugitive emissions include ancillary operations such as press washing (cleaning) and ink mixing operations. Air emissions from imaging include potential volatile components in the developer (e.g. alcohol) and fixer. Adhesives used in finishing operations such as laminating also may contain VOC and HAP and are a potential source of emissions.
Printing industry pollution is predominantly released into the air. In 1993, the printing industry released 99 percent of its total Toxic Release Inventory (TRI) poundage to the air, while the remaining one percent of releases were split between water and land disposal. The four top toxic chemicals released, toluene, methyl ethyl ketone, xylene, and 1,1,1-trichloroethane, are all solvents of high volatility. By far the single largest toxic chemical used (released/transferred) by the printing industry is the solvent toluene; toluene comprises roughly 70 percent of the total chemicals released and transferred by the industry (in 1993). Toluene is used heavily in the gravure printing process as an ink solvent, but is also used throughout printing for cleaning purposes.
For a more detailed and specific discussion of emissions points from the different printing operations refer to one of the following documents:
Air Pollution Control Techniques
The following two general approaches to emissions control are used in the industry: 1) compliant inks and coatings, and 2) capture and control systems. A combination of these techniques is also sometimes used. The use of compliant coatings involves employing inks and coatings formulated to contain no or low concentrations of pollutants (VOC or HAP); pollution is prevented at the source. Capture and control involves capturing the emissions from the source and directing the emissions to an add-on control system (air pollution control device). Below are several links to detailed information on air pollution control technologies typically used in printing operations. Specific control technologies may be used in certain types of printing, but not others.
- Compliant (no or low VOC/HAP) Inks and Coatings
- Capture Systems (Permanent Total Enclosures)
- Catalytic Oxidizers
- Carbon Adsorbers (with Solvent Recovery Units)
- Thermal Oxidizers
- Condensers
The following paragraphs briefly discuss control technologies and pollution prevention techniques applicable to various sectors of the printing industry
Offset Lithography
Control system options for driers in heatset web lithographic printing include thermal oxidizers, catalytic oxidizers, condenser filters with activated carbon and condenser filters without activated carbon. Fountain solutions for lithography are typically refrigerated to reduce volatilization during the printing process.
Flexography
In flexography, emissions are most commonly controlled with catalytic oxidation or thermal oxidation. In some cases, add-on air pollution control devices can be avoided completely by using compliant coatings, i.e., low/no-VOC/HAP inks.
Publication Rotogravure and Product Rotogravure
Large publication rotogravure plants typically use carbon adsorption. These presses use a single water-immiscible solvent (toluene) or a simple mixture (toluene-xylene-naptha) that can be recovered in approximately the proportions used in the ink. Recovery is typically performed by flushing with steam, and then subsequently condensing and separating the condensed water from the solvents.
At present, only solvent-borne inks are used on a large scale for publication rotogravure printing. Waterborne inks are still in research and development phases, but some are now being used in limited cases.
Some smaller rotogravure operations, such as those that print and coat packaging materials, use complex solvent mixtures in which many of the solvents are water soluble. Thermal or catalytic oxidation is usually the most feasible control for such operations.
In addition to thermal and catalytic oxidizers, pebble bed oxidizers are also available. Pebble bed oxidizers combine the functions of a heat exchanger and a combustion device and can achieve a heat recovery efficiency of 85 percent.
Letterpress Printing
Letterpress publication printing uses a variety of papers and inks that lead to emissions control problems. Losses can be reduced by thermal or catalytic oxidation, either of which may be coupled with heat recovery.
Screen Printing
Both thermal and catalytic oxidizers are in use on screen printing drier exhausts for solvent borne ink systems.
Monitoring Information
There are numerous sources of monitoring information available. Some of the information sources address general monitoring approaches and techniques; others are specific to this industry. Click the link below for more information on monitoring.
Learn more about monitoring specific to printing and publishing
Permits
Monitoring to comply with applicable requirements is an important part of the title V program, as well as NSPS and NESHAP regulations. This section provides links to permit information specific to the printing and publishing industry, as well as to general information related to monitoring for title V permits.
Title V Permits - Printing and Publishing Specific Information
EPA has prepared a Technical Support Document (TSD) for Title V Permitting of Printing Facilities.
Title V Permits - General Information
EPA has a specific website for title V related information. Also many states have web sites established for title V permit information. In some cases, the state website will provide a list of draft and final permits that have been issued; in other cases, the state website will actually allow the user to download a copy of the draft and final permits issued. For this website, a separate page has been developed that focuses on monitoring for permits, including title V permits, and provides links to other EPA and state title V permits:
Monitoring for Title V Permits
Applicable Standard Industry Classifications (SIC) Codes
The printing and publishing industry encompasses numerous Standard Industry Classifications (SIC). A summary table of major SIC Codes for the industry can be found at the link below. If you are looking for information to identify the industry associated with a particular SIC, a complete listing of SIC Codes can be found at the SIC website.
Source Classification Codes (SCC)
Printing and Publishing SCCs can be found in section 4-05 in FIRE Version 5.0 Source Classification Codes And Emission Factor Listing for Criteria Air Pollutants(255 pp, 7.6 M, About PDF), August 1995, EPA 454/R-95-012.
Applicable North American Industry Classification System (NAICS) Codes
Regulations
Links to National Emission Standards for Hazardous Air Pollutants and New Source Performance Standards for the Printing and Publishing Industry are listed below.
The following links go to the GPO eCFR website:
Related Industry Regulations
The following links go to the GPO eCFR website: