Success Stories from the PCB Cleanup and Disposal Program
The environmental projects listed below showcase some of the accomplishments of EPA's PCB Cleanup and Disposal Program.
On this page:
- AK Steel's Cleanup of Dicks Creek and Monroe Ditch
- Boeing Corporation Cleanup
- Former Lawrence Metals Site
- Seaholm Power Plant Cleanup
- Kurion’s PCB/Radioactive Waste Mobile Disposal Unit
- Florida Transformer Inc.'s Mobile Disposal Unit
- TD*X Associates, LP's Treatment Unit
- Additional Success Stories
AK Steel's Cleanup of Dicks Creek and Monroe Ditch - Middletown, Ohio
Site Description:
Dicks Creek and its Monroe Ditch tributary, which ultimately flow into the Great Miami River, are located along the southern border of Middletown, Ohio. Portions of AK Steel’s Middletown Works facility are adjacent to these bodies of water.
Background:
The creek was once a popular spot where adults and children fished and swam. AK Steel produces flat-rolled carbon, stainless and electrical steel products, and carbon and stainless tubular steel products for the automotive, appliance, construction and manufacturing markets. In 1997, EPA inspectors found PCBs leaking into Dicks Creek from a holding pond at AK Steel’s Middletown Works, and Ohio inspectors detected PCBs at a concentration of 2.702 µg/L (ppb) in surface water. Ohio's water quality standard for PCBs in surface water is 0.00079 µg/L.
Contamination:
In 2000, the U.S. EPA, Ohio EPA, and two citizens’ groups sued the steelmaker for violating the federal Clean Water Act, the Clean Air Act, and the Resource Conservation and Recovery Act, along with Ohio environmental regulations. The lawsuit charged that AK Steel had, for years, illegally discharged PCBs into Dicks Creek, which is part of the Mississippi River watershed. The lawsuit was settled in 2006 when AK Steel entered into a Consent Decree with EPA.
Cleanup:
The cleanup of PCBs from Dicks Creek was coordinated between the RCRA Corrective Action and Toxic Substances Control Act (TSCA) PCB programs. As part of the remediation of the creek, AK Steel collected and analyzed soil samples according to an EPA-approved TSCA PCB cleanup plan. AK Steel then disposed of soil with high levels of PCBs and restored the area with clean soil, gravel and native vegetation along the creek. It is estimated that AK Steel spent more than $17 million in remediation work.
Boeing Corporation Cleanup - Everett, Washington
Site Description:
The Boeing Company owns and operates the Boeing Everett Plant at 3003 West Casino Road in Everett, Wash.
Background:
The plant produces model 747, 767, 777 and 787 commercial aircraft. In 2000, Boeing began replacing joints separating large concrete slabs that make up the plant's flight line, where planes are parked for final testing before being delivered. The joints, which allow the concrete to swell and shrink as temperatures change, contained a PCB-contaminated sealant. (The joints are part of the original 1960 plant construction; most PCB manufacturing, processing, distribution in commerce, and use was banned in 1979). Old PCB transformers and substations also were found at the site in building 40-83, which was remediated under a separate approval in 2015.
Contamination:
Over time, the hazardous substances from the facility contaminated concrete, soils, groundwater, surface water and sediments. These hazardous substances included:
- Chlorinated solvents (like TCE and PCE);
- Non-chlorinated solvents;
- Fuels;
- Oils;
- PCBs; and
- Heavy metals.
Stormwater contaminated with PCBs from the deterioration of joints sent PCBs into the nearby Powder Mill Creek, which discharges into Possession Sound. Boeing also planned for the demolition of building 40-83 to build the new 777 composite wing manufacturing facility. This building contained two old substation rooms in the basement, which were contaminated with PCBs from the former transformers. PCBs also contaminated underlying soils.
Cleanup:
EPA and the Washington Department of Ecology approved Boeing’s plan for concrete joint material removal, as well as the disposal and remediation of concrete and soils associated with building 40-83.
Concrete Joint Material is an ongoing, multi-year project. While removal is underway, the Washington Department of Ecology required Boeing to improve the way it collected stormwater running off the flight line. Boeing changed how water is discharged from its retention pond. In a plan approved by EPA and the state, the new stormwater management system allows sediment, including sediment contaminated with PCBs, time to settle out of the water before the water is discharged into Powder Mill Creek. The PCB-contaminated sediment from the stormwater basin is now removed and taken to a facility designed to handle toxic waste.
Disposal and cleanup of the former building 40-83 was relatively straightforward as a typical dig-and-haul activity. Additionally, during building 40-83 demolition and cleanup, Boeing was the first facility to implement the American Society for Testing and Material’s Greener Cleanup Standard at a PCB remediation site. Implementing Greener Cleanup[1] practices allowed the cleanup to go beyond removing PCBs to also reducing the environmental footprint of the cleanup; to minimize total energy use and maximize use of renewable energy; to minimize air pollutants and greenhouse gas emissions; to minimize water use and impacts on water resources; to reduce, reuse and recycle material and waste; and to protect land and ecosystems.[2] The remediation of building 40-83 was also completed in a very short time—approximately two months from when the proposed plan was submitted to EPA to the submission of the completion report. EPA and the Washington Department of Ecology worked to streamline the approval process in order to support the redevelopment of this part of the site for the new 777 composite wing facility.
Former Lawrence Metals Site - Chelsea, Massachusetts

Background:
The site had been previously used for various commercial and industrial uses, such as textile production, since the late 19th century. The most recent uses of the site included the manufacturing and custom fabrication of various metal products. In 1999, the City of Chelsea acquired the property under an Urban Renewal Plan, and in December of 2000, it demolished the Lawrence Metals building, leaving only the foundation and floor slab. The site remained vacant for over a decade.
Contamination:
During the planning stages of a Brownfields cleanup, PCBs were detected in soil samples at the site at levels as high as 208,000 mg/kg. Concentrations at the site exceeded the default cleanup standards considered protective of public health (1 mg/kg; 10 to 100 mg/kg if a compliant cap is used).
Cleanup:
In July 2012, the Massachusetts Department of Environmental Protection requested EPA's assistance in conducting a removal site evaluation for a cleanup action. EPA mobilized in July 2013 and began the excavation and removal of over 9,000 tons of PCB-contaminated soil from the site. The cleanup was completed in August 2014.
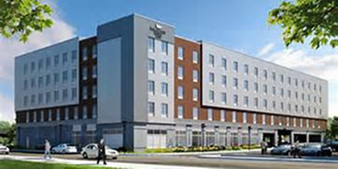
EPA achieved a far more protective level of cleanup by working closely with all of the parties, government and private, who contributed funds and expertise to the overall cleanup. EPA provided $1.5 million in funding for the cleanup, Lawrenceville LLC contributed $1.4 million, and the City of Chelsea contributed $250,000 in a MassDevelopment loan. The EPA team included a coordinated effort by its cleanup programs: the TSCA PCB Program, Brownfields, and Superfund. With a construction cost of more than $30 million, the new hotel and event center built on the site will serve the demand for area lodging; provide meeting and function space that was absent in the community; expand the community tax base; and provide permanent jobs to local residents.
In 2017, all the federal, state, local and private entities involved in the transformation of the former Lawrence Metals site were recognized with the James D.P. Farrell Award for the Brownfields Project of the Year from the Environmental Business Council of New England for “outstanding environmental and energy accomplishments in the promotion of a sustainable, clean environment” and for serving as “an example of excellence notwithstanding the social, economic, technical and institutional challenges imposed.” View the press release for more information on this (pdf)(221 KB).
Seaholm Power Plant Cleanup - Austin, Texas

Site Description:
The Seaholm Power Plant was an Austin city-owned power generation facility that sat on an eight-acre site on the north shore of Town Lake in downtown Austin, Texas.
Background:
The plant was constructed in two phases, in 1950 and in 1955. It operated as a power plant for the city until 1991. In 1996, the Austin City Council authorized the decommissioning of the plant and agreed to preserve the Seaholm Power Plant for public use after it was decommissioned.
Contamination:
Sampling identified soil contamination from PCBs, semi-volatile organic compounds, arsenic and lead. During the initial remedial action, 30,000 cubic yards of waste was removed from the site. Following that action, confirmation soil sampling in the plant’s equipment storage yard showed PCBs at more than 50 mg/kg. PCB contamination was also in the concrete floors in the plant’s turbine building.
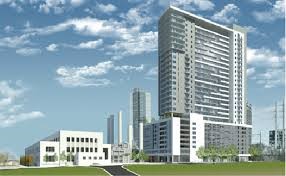
Cleanup:
The remediation of the Seaholm Power Plant site was accomplished through close cooperation between EPA’s cleanup programs (PCB Cleanup and Disposal Program and RCRA Corrective Action) and Brownfields, the Texas Commission on Environmental Quality (TCEQ) , and the city of Austin.
EPA was able to negotiate an innovative way to address some of the PCB-contaminated floors by covering the floor with fiber-reinforced epoxy. Since the Seaholm Power Plant was envisioned to be used as a public space for people of all ages, the PCB-contaminated concrete floors needed to be isolated from the public, but at the same time, not removed to the point that the integrity of the building was damaged. By identifying the PCB-contaminated areas through sampling and analysis, EPA was able to work with the contractors to approve a plan for the fiber-reinforced epoxy that protects the public while maintaining building integrity.
After the successful excavation, removal and disposal of the PCB-contaminated soils, TCEQ issued a Certificate of Completion. In 2006, TCEQ and EPA deemed Seaholm “Ready for Reuse.” The Seaholm plant was the first facility nationwide to receive this designation under TSCA after a nine-year, $13 million cleanup of PCBs and other hazardous materials. By awarding “Ready for Reuse” designations, EPA hopes to encourage other cities and states to invest in PCB cleanup projects that will benefit communities, as well as the environment.
In the years that followed the cleanup, a $130 million redevelopment investment has created 143,151 square feet of office space; 280 high-rise condos; and 48,363 square feet of retail shops, restaurants and meeting space—all surrounding an accessible plaza.
Kurion's PCB/Radioactive Waste Mobile Disposal Unit -Richland, Washington
Background:
Wastes that contain regulated levels of multiple contaminants must be disposed of in a way that controls the risks from all contaminants. Kurion, Inc. out of Richland, Wash., designed an innovative mobile disposal unit to treat PCB-contaminated radioactive waste. After Kurion developed this new technology, they applied to EPA for an operating approval. EPA regulates the treatment of PCB-contaminated waste, while the Nuclear Regulatory Commission regulates the treatment of radioactive waste. EPA only issues an approval after finding that the alternative disposal technology destroys PCBs just as well as or better than incineration, and does not present an unreasonable risk of injury to human health or the environment.
Technology Description:
The GeoMelt In-Container Vitrification (ICV) unit uses a large lined container (similar to a dumpster in size) to treat contaminated soil, waste or debris. First, the waste-filled container is uniformly heated until the temperature is above the melting point of the waste. Then the container is slowly cooled back to room temperature, converting the contents of the container into an inert and stable glass-like product. Any gases produced during the treatment process are captured and managed by the off-gas treatment system (OGTS). The OGTS filters, scrubs, cools and thermally treats the captured exhaust gases prior to release into the environment.
Application Review and Demonstration:
After extensive review of the application, EPA approved Kurion to perform a demonstration of the GeoMelt ICV unit supervised by EPA personnel. Based on the results from the demonstration, as well as Kurion’s operating procedures and safety precautions, EPA determined that the extreme temperatures used in the GeoMelt ICV destroy the PCB molecules to a level that is equivalent to that of an incinerator. EPA approved Kurion, Inc. to operate their mobile GeoMelt ICV unit anywhere in the United States to treat/destroy PCBs in contaminated soil, waste and debris. By issuing this PCB approval, EPA is helping to ensure the proper disposal of PCB-contaminated waste, which limits the exposure of humans and the environment to PCBs. This approval also helps ensure that PCB waste is managed in a way that minimizes risks and helps prevent PCB releases from spills, fires, explosions and improper management practices in general.
Florida Transformer Inc. Mobile Treatment Unit - Defuniak, Florida
Background:
EPA approved Florida Transformer Inc. (FTI) to operate its mobile chemical dechlorination unit, the PCB-1000 Chemical Dechlorination (CD) unit, to treat/destroy PCBs in Mineral Oil Dielectric Fluid (MODEF), which is found in electrical equipment such as transformers and electrical switches.
Technology Description:
FTI's mobile PCB-1000 CD unit uses a chemical process that destroys PCBs with the use of a sodium reagent. In this process, the sodium reagent reacts with the chlorine atoms on the PCB molecule to form sodium chloride and chlorine-free biphenyl molecules.
The PCB-1000 CD unit can be divided into five separate components: degasifier, reagent system, mixing tanks, centrifuge and nitrogen purge system. Generally, PCB-contaminated mineral oil dielectric fluid is transferred from a bulk tank to the PCB-1000 CD unit, after first passing through a degasifier and heater to remove moisture and other vapor. The degassed oil enters the two mixing tanks and is heated to the proper reaction temperature, and is continuously agitated to achieve proper mixing, reagent dispersion and reaction. After a certain reaction time, the treated oil is passed through an air cooler component to lower the temperature of the oil, further quenched with water, and transferred to the centrifuge. The centrifuge then removes sludge byproduct consisting of chlorine-free biphenyl molecules and salt.
The advantage of FTI’s technology is that it destroys the PCBs in the contaminated oil and allows the MODEF, after some additional processing, to be recycled back into the oil market.
Application Review and Demonstration:
After extensive review of FTI’s application, EPA approved FTI to perform a demonstration of the CD unit under the observation of EPA personnel. EPA then reviewed the results from the demonstration, as well as FTI’s operating procedures and safety precautions. EPA confirmed that the chemical reagent in the CD unit destroyed the PCB molecules to a level that is equivalent to that of a PCB incinerator. Following a successful demonstration of FTI technology, EPA approved FTI to dispose of PCBs and set forth the approval conditions based on the parameters FTI used in its technology demonstration. By issuing this PCB approval, EPA ensures that this technology effectively destroys PCBs and that the recycled oil can be safely reused. In addition, EPA ensures that the conditions of the approval minimize the risk of any releases during operation of the unit.
TD*X Associates, LP's Treatment Unit at the EnergySolutions, Inc. Facility - Clive, Utah
Background:
The EnergySolutions facility receives waste that is both PCB-contaminated and a mixture of radioactive and hazardous waste (known as “mixed waste”). Multiple regulatory frameworks apply to these wastes: Radioactive wastes are regulated under the Atomic Energy Act, PCB-contaminated wastes are regulated under the Toxic Substances Control Act (TSCA), and hazardous wastes are regulated under the Resource Conservation and Recovery Act (RCRA). For this site, the Utah Division of Waste Management and Radiation Control (DWMRC)regulates mixed waste operations and EPA regulates PCB wastes.
EPA approved TD*X Associates LP (TD*X) to operate its High Performance Indirect Thermal Desorption Unit (HP-TDU) at the EnergySolutions facility in Clive, Utah. The HP-TDU thermally removes PCBs from low-level radioactive and hazardous waste, which includes solidified liquids, soil, pumpable sludge, sludge, waste oil, blended feed materials, debris, shredded capacitors and other metallic surfaces that are generated from Department of Energy operations, such as cleanups of radioactive sites.
Technology Description:
In the thermal desorption process, the contaminated materials are heated to a high temperature in an atmosphere of nitrogen so that any organic solvents and PCBs present are removed by heat, followed by condensation (cooling the vapor and collecting them in drums). The resulting solid residues (treated solid) contain no more than two ppm PCBs, which is the regulatory threshold for successful disposal under the PCB regulations. The condensed organics and PCBs in the resulting oil are then sent to a PCB incinerator for treatment.
The advantage of thermal desorption is that it removes the organics and PCBs from the radioactive waste materials, thus reducing its volume substantially before it is sent to the onsite landfill. As an additional benefit, the HP-TDU unit is designed to be suitable for the treatment of radioactive waste, as regulated by the Nuclear Regulatory Commission.
Application Review and Demonstration:
After extensive review of TD*X’s application, EPA approved TD*X to perform a demonstration of the HP-TDU unit, under the observation of EPA and state of Utah personnel. EPA then reviewed the results from the demonstration, as well as TD*X’s operating procedures and safety standards. EPA determined the high temperatures used in the HP-TDU remove the PCB molecules from the contaminated media to a level that is equivalent to that of an incinerator. During the demonstration, EPA also confirmed that the volatilized gas, which is sent through a bank of carbon filters and then vented to the atmosphere, contains essentially no detectible PCB or organic air emissions. Following a successful demonstration of TD*X technology, EPA approved TD*X to dispose of PCBs and set forth the approval conditions based on the parameters TD*X used in its technology demonstration. By issuing this PCB approval, EPA ensures that the technology effectively removes the PCBs from the waste without posing unreasonable risk to health and the environment.