10 Keys to Digester Success
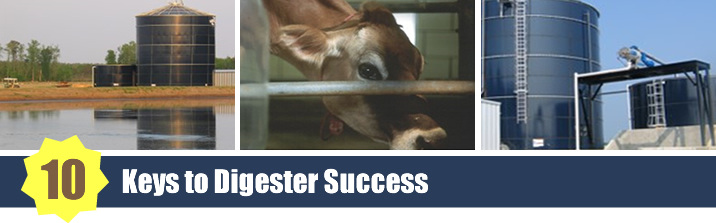
Many factors are required to successfully implement and operate an AD/biogas system. The following list briefly introduces the 10 key factors essential for a successful farm-based digester project. Click to learn more.
- Plan for success.
During the planning stage, identify and define clear project goals. To establish these goals, site-specific farm information should be collected, including ownership and managerial goals and projections, animal information (e.g., number, types, maturity, bedding type), type(s) of manure recovery, volume of manure, manure analytical information, past and current disposal practices, and operational costs. Working towards project parameters is also crucial in addressing and meeting goals. This includes, often in iterative planning stages, identifying available feedstock, defining the type of digestion system, conversion efficacy of that feedstock, economic or financial factors and limitations, and project risks associated with developing an AD/biogas system.
- Recruit and secure an experienced team.
Seek out and work with an experienced and qualified team to help initiate and successfully implement the project. At project initiation, the “core” team should include:
- an engineer/permitting specialist who knows the farm history and local regulations and
- an engineer or specialist with seasoned experience implementing various AD/biogas systems.
Verify the project references, experience, and historical success of the engineers and specialists. This “core” team should help identify an applicable system and ensure the development is feasible and planned to meet the owner’s goals and expectations. As the project progresses, the team may also expand to include technology vendor(s), equipment provider(s), a project developer, investors/bankers/lender(s), and/or operators to supplement the initial “core” team. The farm owner or operating personnel should also be included in the “core” team early on if the project is not being developed by the farm itself.
- Develop a sustainable business model.
A successful AD/biogas system requires a sustainable business model. The project should not only be cost-effective, but it must also meet financial goals. The economic factors include well-defined project costs, expenses, revenue or income, liabilities, among many others. Personal goals for the project’s liquidity and profitability potential define the financial factors. The business model could consider involving partners, utilizing third party investments, or other traditional ‘cooperative’ models.
- Secure suitable feedstock supply.
During the planning and engineering phase, identify all suitable feedstocks. The digester must be supplied with a consistent quality and type of feedstock (manure and co-substrates) to maintain a productive microbial community. This will result in consistent organic destruction and biogas production and minimize operational issues. It is of high value to ensure that feedstocks are free of toxic and inorganic contaminants that will “upset" the intended microbial and mechanical processes. Sand, gravel, and other inert material should be removed to the degree possible to minimize sediment accumulation in the digester. Feedstocks from outside sources should be routinely characterized to monitor consistency. Projects that focus on co-digestion feedstocks (i.e., feedstock supplementing manure) should include contractual agreements to specify material quantity and quality, testing frequency, revenue received, and duration to ensure the right type and amounts of materials and revenue are provided. Co-digestion feedstocks should be designed for flexibility as external supplies are likely to vary over time.
- Use the most appropriate technology.
The AD technology needs to be carefully evaluated to match the type and amount of feedstock that is expected to be processed. There is no single AD technology that can be used for all situations or feedstock.
Among the many key factors that need to be considered include:
- the type of manure and co-digestion feedstocks,
- how the manure is collected,
- conversion efficiency goals,
- the climate where the digester is located,
- bedding type and mass,
- amount of allocated maintenance, and
- other factors.
AD technology selection should also consider management goals and needs and future plans of the farm.
- Analyze options for biogas and digestate use.
During the planning stage, considerations should include market availability, capital and operating costs, and potential revenue to determine how the biogas is best monetized, which can include on-site use or off-site sales.
Potential uses include:
- on-site use of thermal and/or electrical energy,
- off-site sale of thermal and/or electrical energy,
- off-site sale of compressed natural gas or liquified natural gas (CNG/LNG) typically used for transportation fuel or other applications,
- on-site use of renewable natural gas (RNG),
- off-site sale of RNG, and/or
- bio-based material generation.
The need for on-site digestate use as fertilizer or bedding should also be determined, and the market for digestate final products should be assessed, including fertilizer, salable compost, or other value-added digestate products. Proper management of digestate, whether recovered for its nutrient value or disposed of in an environmentally correct manner, is critical to the success of the project.
- Develop off-take agreements.
It is critical to execute off-take agreements or legal contracts with users of the AD/biogas products and byproducts (e.g., biogas, electricity, heat, RNG, digestate, fertilizers) early in the development stage. These agreements—including power purchase agreements (PPA), biogas/RNG sale agreements, or digestate sales agreements—define the price and detailed specifications for all materials that any third party will purchase.
- Evaluate added benefits.
Consider the added benefits of AD, which may be difficult to quantify, but could be critical reasons for implementing an AD/biogas project. These benefits may include odor control or reduction in greenhouse gas (GHG) emissions. Digesters often are installed to reduce odor problems, particularly on farms where there is public development encroachment.
- Conduct community outreach.
Community outreach and education is critical to obtain buy-in and approval from the community, including, but not limited to, regulatory approval and the community and neighborhood approval where the project is located.
- Plan for operation and maintenance.
Good operation and maintenance practices are key for effective operation of AD/biogas systems. This includes continuous monitoring and management to ensure the biological processes and mechanical equipment are working properly. Often, AD/biogas system operating expenses (OPEX) are underestimated. Analyzing other similar operating systems that have several years of operational history can assist in predicting OPEX accurately. It is also important to consider whether current staff or a third party will be used to perform these functions.
For more information about the "10 Key Steps to Digester Success" visit: AgSTAR's Anaerobic Digester Project Development Handbook.
Also, see the Risk Analysis and Technical Review Checklist for Preparing Biogas Project Plans, which can help project developers, government agencies, financial institutions, and other stakeholders assess the technical and financial feasibility of a proposed AD/biogas project.