Project Planning and Financing
Assessing the financial feasibility of an anaerobic digester (AD)/biogas project is an iterative process. The first step is to do preliminary project planning. In this step, you do preliminary screening and a technical feasibility assessment to determine if the project can technically work. Then, using those assumptions, you can develop a high-level estimate of the project’s financial feasibility and return on investment considering revenues and expenses. During the planning phase you also review potential owner/operator models for your AD/biogas project and financing options (if needed). Once project planning is complete, you will likely need to refine your assumptions to optimize technical and financial performance with a new project plan before you are ready to implement your project.
Preliminary Screening
Determine whether anaerobic digestion is right for you by considering:
- manure availability,
- whether your manure management technique is compatible with an anaerobic digester,
- potential uses for recovered energy and
- whether you have the capacity to manage the system.
See chapter 7 of the AgSTAR Project Development Handbook for more information about project screening. Chapter 12.5 also lists resources that provide information related to AD project screening and feasibility studies.
EPA’s Anaerobic Digestion (AD) Screening Tool can also assist stakeholders in assessing the potential feasibility of an AD project. The AD Screening Tool enables users to conduct pre-feasibility analyses to evaluate AD opportunities for a variety of feedstocks, including organic municipal solid waste, livestock manure, agricultural residues, and wastewater.
Technical Feasibility
Start assessing your project’s technical feasibility by identifying the anaerobic digester components:
- feedstock,
- onsite conditions,
- system type and size, and
- biogas use.
See chapter 7 of the AgSTAR Project Development Handbook for more information about assessing technical feasibility. Chapter 12.5 also lists resources that provide information related to AD project screening and feasibility studies.
Financial Feasibility: Revenue and Expenses
Revenues
Estimate the annual revenue you could receive from your project based on the anaerobic digester components identified in your technical feasibility analysis. A number of revenue sources can be derived from an AD/biogas system, including:
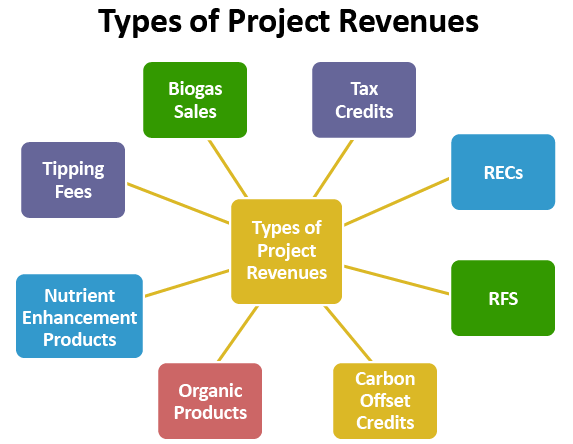
- Biogas sales. Revenue from the sale of biogas can take many forms. For example, biogas used onsite in a combined heat and power (CHP) system will offset a farm’s electricity and heating costs. In some state, farms can sell biogas-generated electricity to the electricity grid. If the farm is producing on-site RNG, then the revenue comes from using the RNG on site, injecting it into a pipeline, or selling it as a transportation fuel.
- Tax Credits. AD biogas systems can qualify for state and federal tax credits (e.g., the federal Renewable Electricity Production Tax Credit, the federal Business Energy Investment Tax Credit).
- Renewable Energy Certificates (RECs). Many states have some form of a renewable energy portfolio standard and many electric utilities are buying Renewable Energy Certificates (REC) for compliance. RECs are tradable, non-tangible energy commodities representing proof that 1 MWh of electricity was generated from a qualified renewable energy resource.
- Renewable Fuel Standard (RFS) and Low Carbon Fuel Standards (LCFS). The federal RFS provides financial incentives for RNG that is used as a vehicle fuel that can be much greater than the value of the gas. Several states have created complementary programs to the federal RFS. These state programs are also focused on the reduction of fossil fuel-based fuel. For example, California and Oregon have LCFS and Clean Fuels incentive programs, respectively.
- Carbon Offset Credits. In some voluntary markets in the United States, carbon offset credits may be earned by reducing GHG emissions, such as the CH4 recovered from an AD/biogas system. These credits have an economic value and can be bought and sold on commodity exchanges, through private transactions, or through credit aggregators. Besides serving as an additional revenue source, carbon offset credits can also provide incentives for outside parties to provide project funding for AD/biogas systems.
- Organic Products. Digested fibrous materials can be used as bedding material, soil amendment product, or to create new products such as CowPots™ and building materials. This material represents a cost offset if used onsite or a revenue source if sold to a third party.
- Nutrient Enhancement Products. Recovery of nutrients from digested manure is of increasing value, as the quality of the nutrients can be easily utilized by plants and can be applied directly without burning crops (when compared to undigested manure). Recovery and selling of nutrients, such as nitrogen and phosphorus, from digested feedstocks is also an emerging opportunity.
- Tipping Fees. Tipping fees received from co-digestion feedstocks are a potential revenue source. Organizations that produce large volumes of waste will often partner with a bidder to off-take their waste. AD/biogas system owners that win these bids can generate significant revenue from the tipping fees associated with accepting these wastes.
See chapter 6.3 of the AgSTAR Project Development Handbook for more information about AD/biogas project revenues.
Expenses
Estimate the annual expenses associated with your project. Include one-time (capital) and ongoing annual (operation and maintenance) costs of the system.
See chapter 6.1 of the AgSTAR Project Development Handbook for more information about capital investment and chapter 6.2 for more information about operating expenses.
Calculate Return on Investment
Compare the annual revenue against expenditures to estimate when the initial investment will be paid back and the rate of return on the money invested. Methods include:
- Payback: the number of years it would take for a project to generate profits equal to the initial capital outlay.
- Discounted cash flow: estimate the net present value of future cash flows.
- Internal rate of return: total rate of return achieved by the project, which can be compared to return rates from alternative investment opportunities.
Revenue and Expenses Tools and Software
The following tools and software are available to help estimate AD/project revenues and expenses.
Tool/Software | Description |
---|---|
Cost of Renewable Energy Spreadsheet Tool (CREST) | An EXCEL-based model assessing project economic feasibility; includes a module specific to AD technologies (National Renewable Energy Laboratory, 2013). |
An Economic Evaluation Tool for Farm-Based Anaerobic Digesters | An EXCEL-based model that assesses farm-based AD/biogas systems in Ontario under different scenarios, such as livestock type, farm size, system operation practices system specifications, government policies, and levels of investment certainty (University of Guelph, with funding from the Ontario Ministry of Agriculture Food and Rural Affairs, 2017). |
Organics: Co-Digestion Economic Analysis Tool (CoEAT) | An EXCEL-based model using publicly-available data to calculate economic, environmental, and operational parameters using food waste as a co-digestion feedstock at a WRRF (EPA Region 9, Pacific Southwest, 2016). |
System Advisor Model (SAM) | A stand-alone performance and financial model designed to facilitate decision making for renewable energy projects. This model is not specific to AD (National Renewable Energy Laboratory, 2010). |
RETScreen Expert | A stand-alone model for determining the technical and economic feasibility of energy efficiency, renewable energy, and co-generation projects. This model is not specific to AD (Natural Resources Canada, 2013). |
AD Budget Calculator | The AD System Enterprise Budget Calculator is intended for dairy owners, AD system industry experts, and AD researchers to help easily calculate the economic value of investments under a variety of technology and price scenarios for an AD system. |
Anaerobic Digestion Financial Decision Tools | This source from Cornell University provides links to a variety of spreadsheet-based financial decision tools. |
Business Model Ownership Structures
Historically, agricultural AD/biogas systems have been owned and operated by the farm. Today, farm-based AD/biogas system projects have many developmental challenges that require more advanced expertise to navigate. As a result, innovative business models are being deployed to share project risk and reward, diversify project revenue sources, and more efficiently develop systems. Determining the business model ownership structure is an important part of planning a project.
Model | Ownership Structure |
---|---|
Farmer owned and operated | A farmer typically owns and operates a digester on site and uses manure from the farm, at a minimum, as feedstock. In some cases, the farmer may accept manure or other organics from off site, generally for a tipping fee. |
Third party owned and operated | A site owner may receive a rental fee or a share of the project's net income, but the third party owns, operates, and invests in the digester. The third party may be a venture capitalist or an investment group specializing in green energy projects. The third party may also manage the feedstock. |
Third party operated | A third party, who does not own the digester, operates the digester, manages feedstock, and manages other aspects of energy and effluent sale. The digester and feedstock can be owned by a single entity or many. |
Hub and spoke | This business model can take two general forms: centralized digester or centralized processing, either of which could be owned by the structures mentioned above, or a municipality. It could also be part of a cooperative, which relies on a voluntary partnership of individuals that jointly own and democratically control the project.
|
See chapter 6.4 of the AgSTAR Project Development Handbook for more information about owner/operator models.
Project Finance
All projects require capital investment, which can be a direct cash equity contribution from the owner, financed with a loan, or both. For projects financed using borrowed money, paying the borrowed principal and interest can be the largest source of the project’s expenses until the debt is retired. Therefore, one or preferably more initial financing cost estimates should be obtained to determine the annualized debt cost the project will incur.
- Owner Equity Financing. Paying for a project with your own cash saves money since you do not have to pay interest to a bank or share the project’s profits with a third party.
- Debt and Equity Financing. Private funding may come in the form of debt financing, equity financing, or a combination of the two. Debt financing involves securing capital from banks, credit unions, savings and loans, or other traditional financial institutions. Equity financing raises funds from third parties to provide up-front capital in return for partial ownership or other valuable considerations.
If you choose to finance your AD/biogas project through debt or equity financing, you will likely be required to invest some of your own equity. A minimum of 10% equity is generally required, but investors and lenders prefer project owners take a higher equity share.
Identify Funding Sources to Fill the Gap Between Your Equity and the Project Cost
The following resources can help you identify grants, loan guarantees and financial assistance from federal and state governments, nonprofits, and private companies.
Resource | Description |
---|---|
Database of State Incentives for Renewables and Efficiency (DSIRE) | The database contains information about renewable energy incentives and policies, which can influence project economic feasibility. |
USDA Energy Matrix | USDA developed this website matrix summarizing USDA's energy-related programs and provides information on alternative and affordable energy solutions, funding for projects, available programs and program information, and research and development. |
USDA Natural Resources Conservation Service | The USDA NRCS provides farmers and ranchers in the United States with financial and technical assistance to voluntarily put conservation on the ground, not only helping the environment, but also agricultural operations. |
USDA Rural Energy for America Program | The USDA REAP provides guaranteed loan financing and grant funding to agricultural producers and rural small businesses for renewable energy systems or to make energy efficiency improvements. Funds may be used for renewable energy systems, such as AD/biogas systems. |
USDA Rural Development Business Programs | USDA's Business Programs provide financial backing and technical assistance to stimulate business creation and growth. |
USDA Rural Development Value-Added Producer Grants (VAPG) | USDA's Value-Added Producer Grant (VAPG) program helps agricultural producers enter into value-added activities related to the processing and marketing of new products. There is an AD-specific portion of this grant. |
AgSTAR Vendor Directory | Includes listings for financing specialists who provide loans for biogas projects, fund on-farm biogas systems for profit and broker the sale of carbon offsets and renewable energy certificates. |
AgSTAR Webinar: Federal Financing Resources for Anaerobic Digesters | Resources from a webinar conducted by AgSTAR and USDA representatives about funding opportunities and support services available to AD/biogas system operators. |
AgSTAR Funding On-Farm Anaerobic Digestion | AgSTAR fact sheet that can help identify grant, loan guarantee, and financial assistance available from federal and state governments, nonprofits, and private companies. |
Sustainable Agriculture Research & Education Grants (SARE) | SARE offers competitive grants to fund research and education projects that advance sustainable agricultural practices in the United States. |
See chapter 6.5 of the AgSTAR Project Development Handbook for more information about project financing.
Refine Project Proposal, Plan and Select Approach
The feasibility of an anaerobic digester project depends on site-specific factors. These factors influence the amount and quality of methane generated, variability in electricity prices, availability of incentives and financing rates. In this stage of project planning, you can go through several versions of project plans, refining your assumptions until you identify the best possible approach for developing and financing your anaerobic digester project.
Some of the key ways to improve project economics include:
- Increasing income from electricity sales (e.g., tariffs for biogas) or other types of energy sales.
- Getting direct financial assistance for feasibility studies and/or up-front costs.
- Using creative financing mechanisms such as tax credits and low interest program investment loans.
- Developing lower cost digester systems.
- Seeking additional revenue-generating options (e.g., finding additional uses for on-farm heat; accepting off-farm wastes for tipping fees; concentrating nutrients for fertilizer products).
- Implementing different business models, such as third party build/own/operate models.