Lean & Energy Toolkit: Appendix C
Energy Conversion Resources and Rules of Thumb for Estimating Energy Cost Savings
- Energy Metrics Conversion Table
- Rules Of Thumb for Estimating Energy Cost Savings
- Toolkit Navigation
Energy Metrics Conversion Table
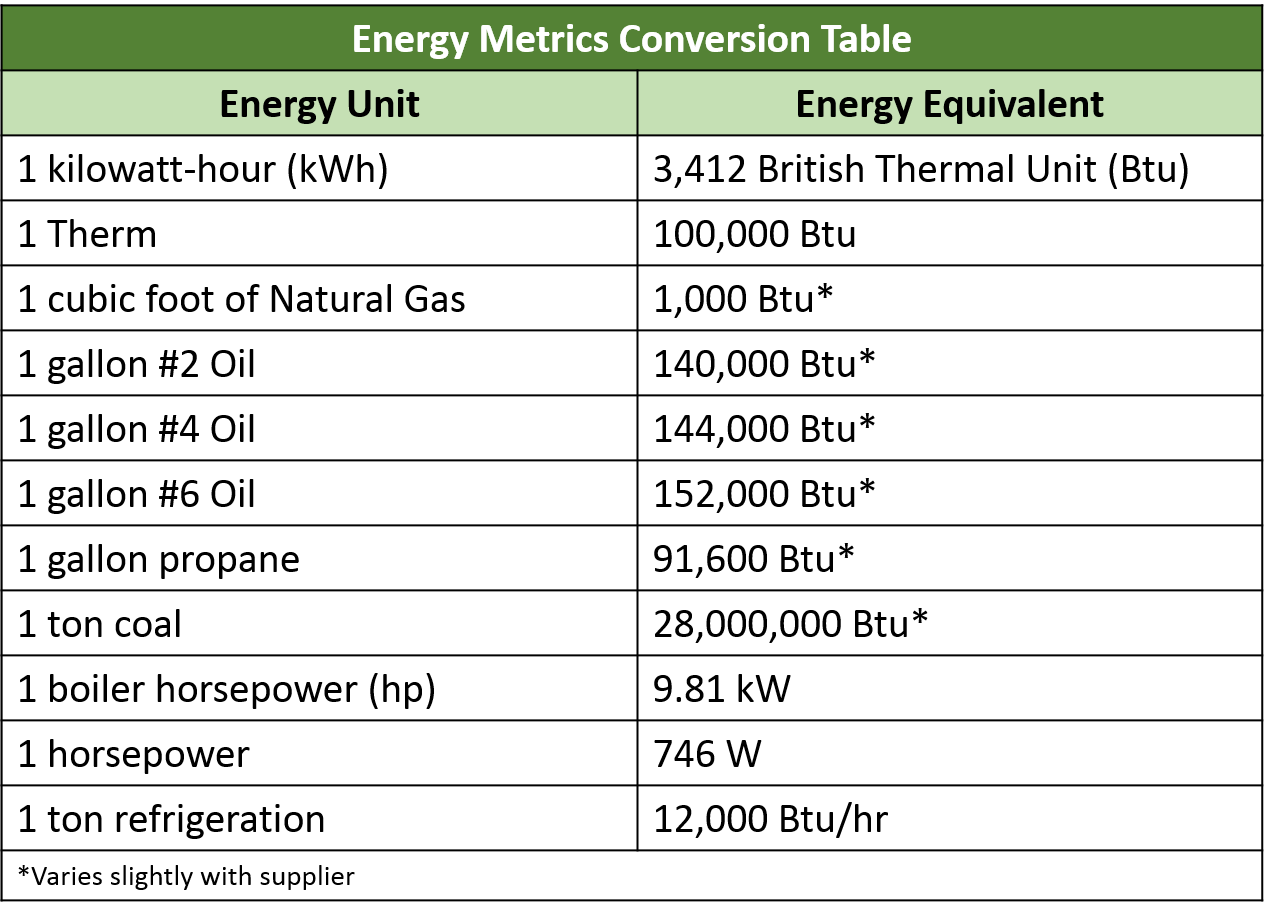
Rules Of Thumb for Estimating Energy Cost Savings
The following rules of thumb are a useful resource for understanding the potential cost savings of energy conservation and waste minimization efforts.

- High pressure steam leaks (125 pounds per square inch gauge [psig]) = $150 to $500 per leak per shift per year.
- Low pressure steam leaks (15 psig) = $30 to $110 per leak per shift per year.
- Compressed air leaks (100 psig) = $30 to $90 per leak per shift per year.
- Submetering an evaporative cooling tower can result in sewage treatment savings (assume 1 percent water loss to evaporation), including:
- $9 per ton per shift per year based on size of tower in tons.
- $3 per gallons per minute (gpm) per shift per year based on gpm of water through tower.
- Typical motor operating cost = $62 per horsepower (hp) per shift per year.
- High pressure compressed air system reduction (assume 100 psig system):
- 10 pounds per square inch (psi) compressor discharge reduction = 5 percent reduction in energy consumption.
- Cost of heat lost through hot, uninsulated pipes:
- 25 psig steam: $375 per 100 feet per shift per year.
- 50 psig steam: $430 per 100 feet per shift per year.
- 75 psig steam: $480 per 100 feet per shift per year.
- 100 psig steam: $515 per 100 feet per shift per year.
- Installing insulation can reduce 90 percent heat loss on a hot, uninsulated surface.
- Average heating and cooling costs:
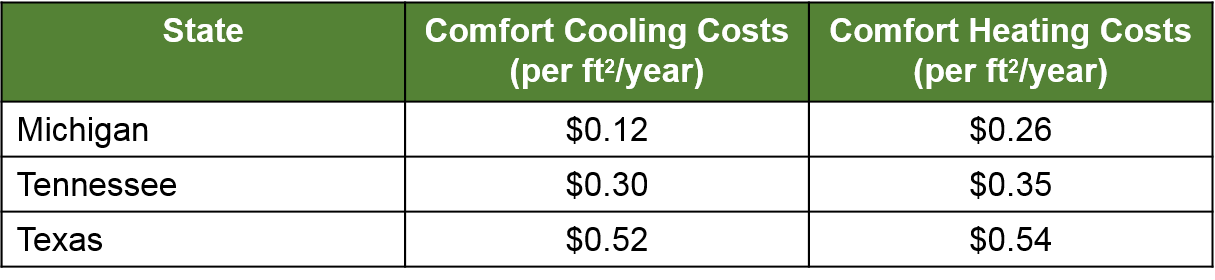
- Combustion efficiency of a typical boiler or furnace is 80 percent.
- Upgrading to an energy-efficient motor can result in savings of about 5 percent over the operating costs of a standard motor. A typical standard motor has an efficiency of 90 percent.
- Benefit of fuel switching:
- Switching from electric heat to natural gas or #2 fuel oil can reduce heating costs by 78 percent.
- Cost savings for demand reduction (or load shifting):
- Move operating shift to off-peak times: $75 per hp per year.
- Move “other electric equipment” to off-peak: $120 per kW per year.
Toolkit Navigation
- Contents & Acknowledgements
- Executive Summary
- Preface
- Chapter 1: Introduction
- Chapter 2: Integrating Lean, Energy Efficiency and Greenhouse Gas Management
- Chapter 3: Overview of Energy Use and Lean
- Chapter 4: Energy and Greenhouse Gas Assessment Strategies
- Chapter 5: Energy and Greenhouse Gas Emission Reduction Tools and Strategies
- Chapter 6: Conclusion
- Appendix A: Energy and Greenhouse Gas Management Service Providers, Resources and Tools
- Appendix B: Sector-Focused Energy Reduction and Greenhouse Gas Management Resources
- Appendix C: Energy Conversion Resources and Rules of Thumb for Estimating Energy Cost Savings