Lean & Energy Toolkit: Chapter 5
Energy and Greenhouse Gas Emission Reduction Tools and Strategies
- Conduct Energy Kaizen Events
- Use Total Productive Maintenance to Reduce Equipment Energy Waste
- Replace Over-Sized and Inefficient Equipment with Right-Sized Equipment
- Design Plant Layout to Improve Flow and Reduce Energy Use
- Encourage Energy Efficiency with Standard Work, Visual Controls, and Mistake-Proofing
- Reduce Greenhouse Gas Emissions through Transportation Efficiencies
- To Consider
- Footnotes
- Toolkit Navigation
Conduct Energy Kaizen Events

Kaizen events create important windows of opportunity to consider ways to eliminate energy waste. Revisit the results of energy audits, assessments or your greenhouse gas inventory to familiarize your Lean team with information that can be used to identify energy wastes during a kaizen event. Asking key questions during a kaizen event, such as those in Box 7, can also help to ensure that energy and greenhouse gas reduction opportunities are identified as part of Lean implementation.
Consider conducting energy-focused kaizen events at your facility to:
- Understand how energy is used in a particular process
- Brainstorm opportunities to reduce energy use in that process
- Implement those ideas in a short time frame
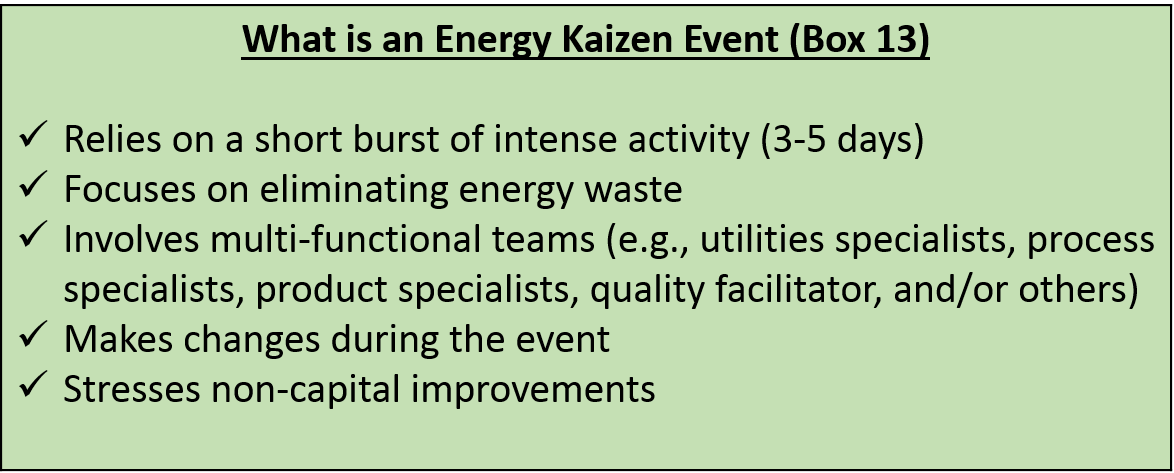

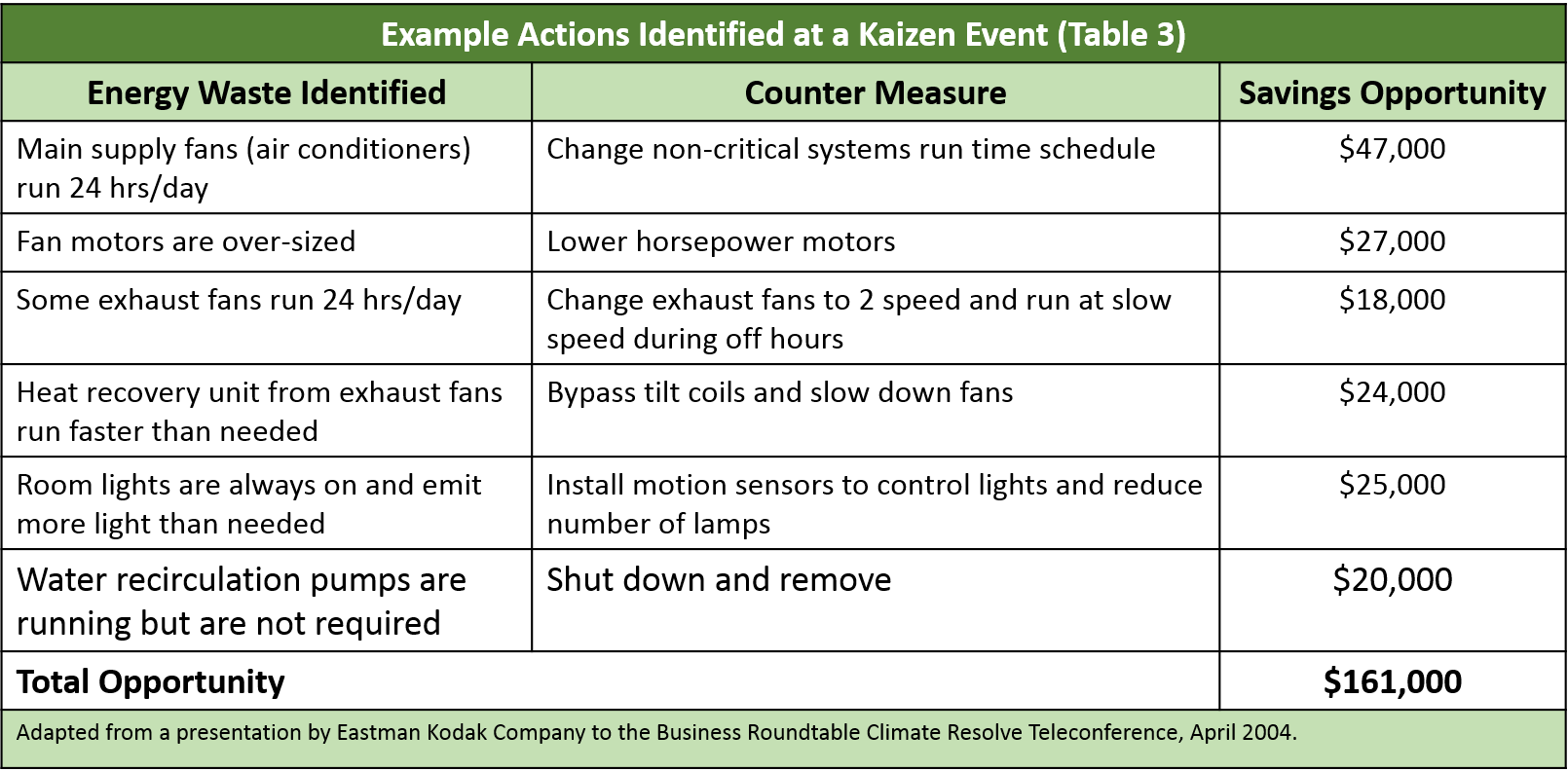
Use Total Productive Maintenance to Reduce Equipment Energy Waste

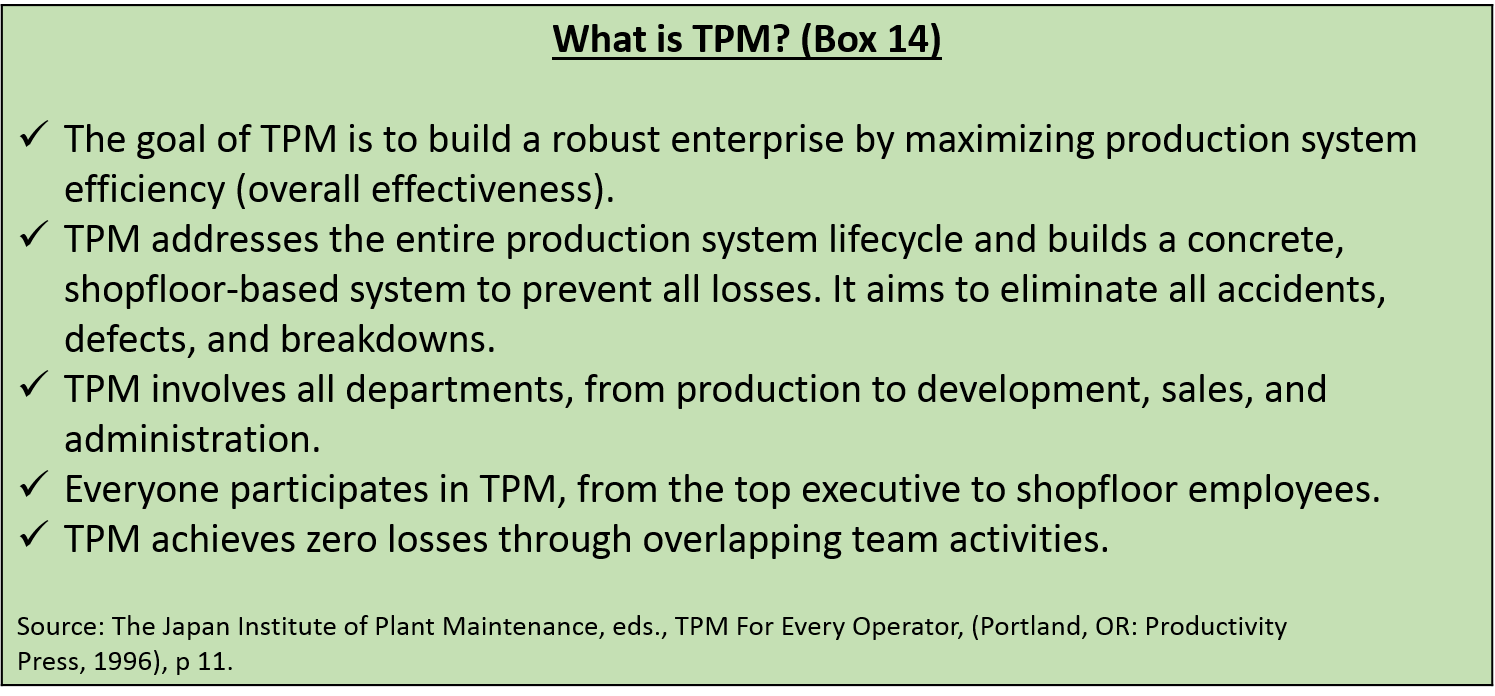
Six Losses That Lower Equipment Efficiency
Increased equipment operating efficiency reduces energy waste. When machines are optimally tuned to accomplish the desired work, energy inputs are most efficient. TPM’s emphasis on equipment efficiency can lead to reduced costs, increased productivity, and fewer defects. TPM focuses on the six big losses that lead to equipment inefficiency:
- Breakdowns
- Setup and adjustment loss
- Idling and minor stoppages
- Reduced speed
- Defects and rework
- Start and yield loss
Eradicating the six big losses maximizes the productivity of equipment throughout its lifetime. With proper equipment and systems maintenance, facilities can reduce manufacturing process defects and save in energy costs.
Consider using one or more of the strategies for integrating energy-reduction efforts into TPM (Box 15) to improve energy and equipment efficiency at your facility. This chapter focuses on describing energy savings opportunities associated with autonomous maintenance (strategy #1); previous chapters of this toolkit provided guidance on identifying energy wastes, conducting energy kaizen events, and developing energy management systems (strategies #2-4).
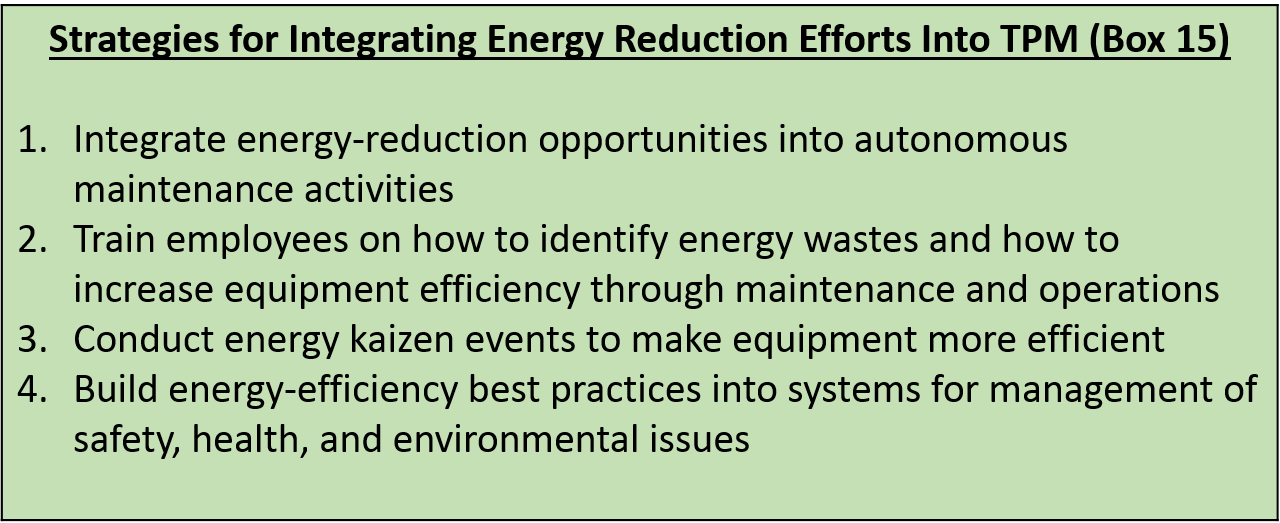
Autonomous Maintenance Improves Energy Efficiency



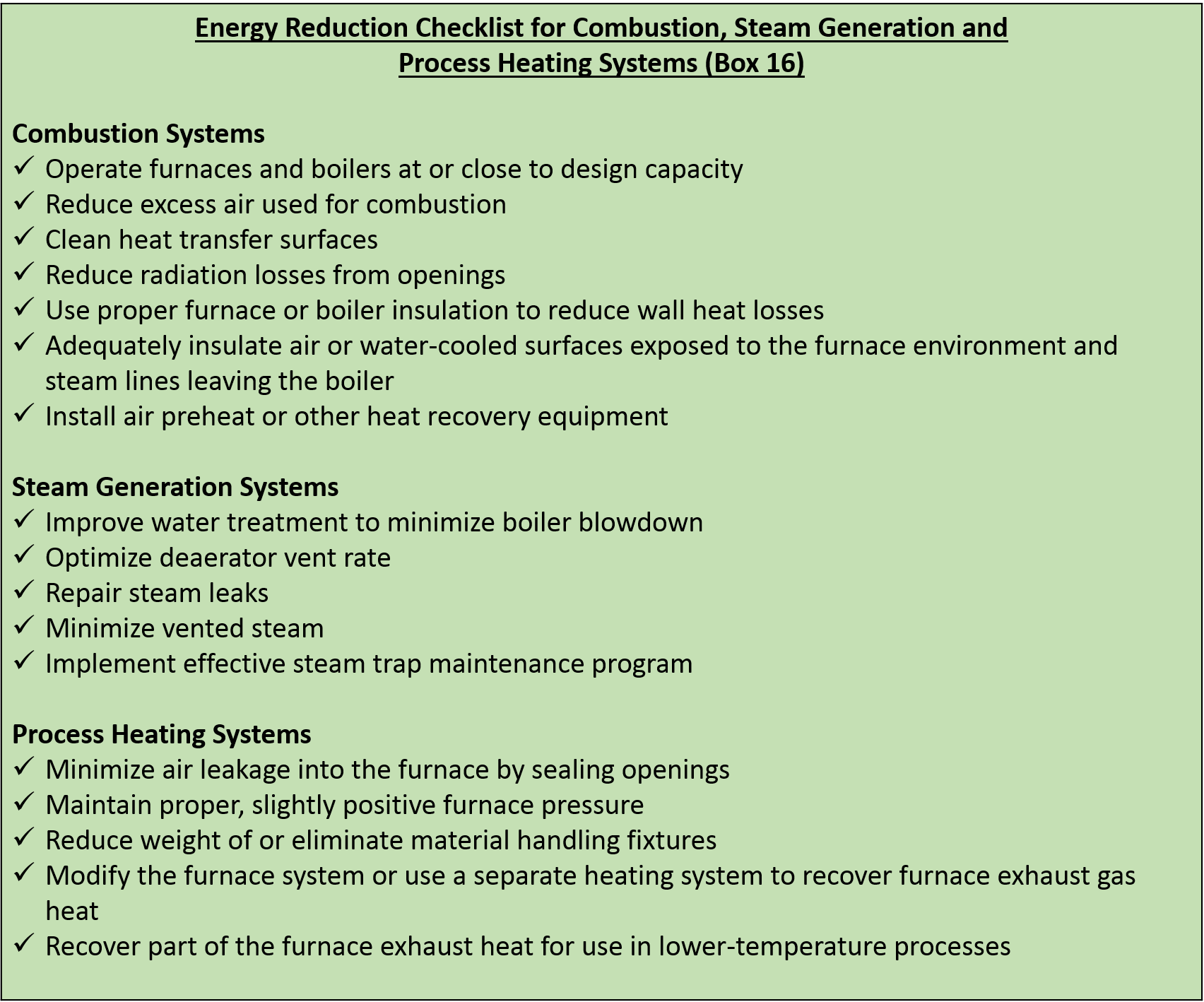
Replace Over-Sized and Inefficient Equipment with Right-Sized Equipment

In conventional manufacturing, equipment is often over-sized to accommodate the maximum anticipated demand. Since purchasing a new large piece of equipment can be costly and time-consuming, engineers sometimes design with an additional “buffer capacity” to be sure that the equipment does not bottleneck production. Box 16 shows results from studies documenting equipment over-sizing.


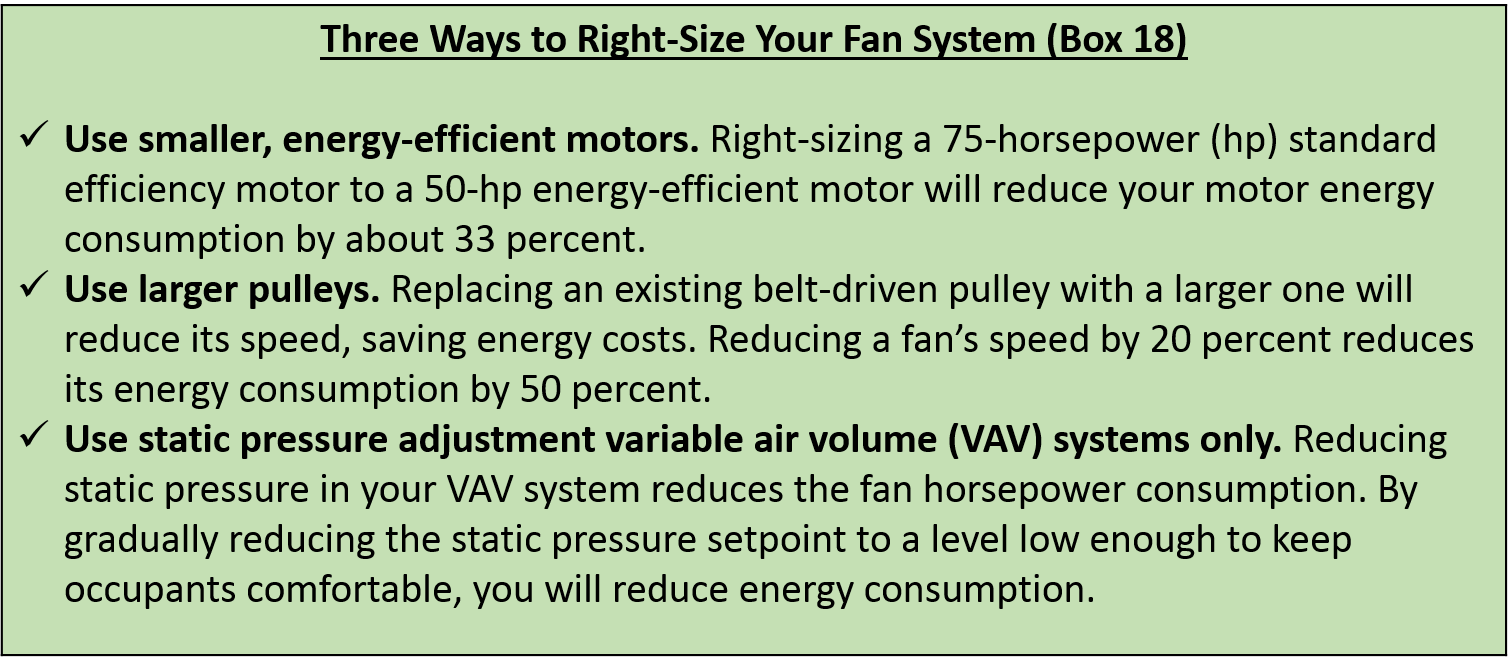
Design Plant Layout to Improve Flow and Reduce Energy Use

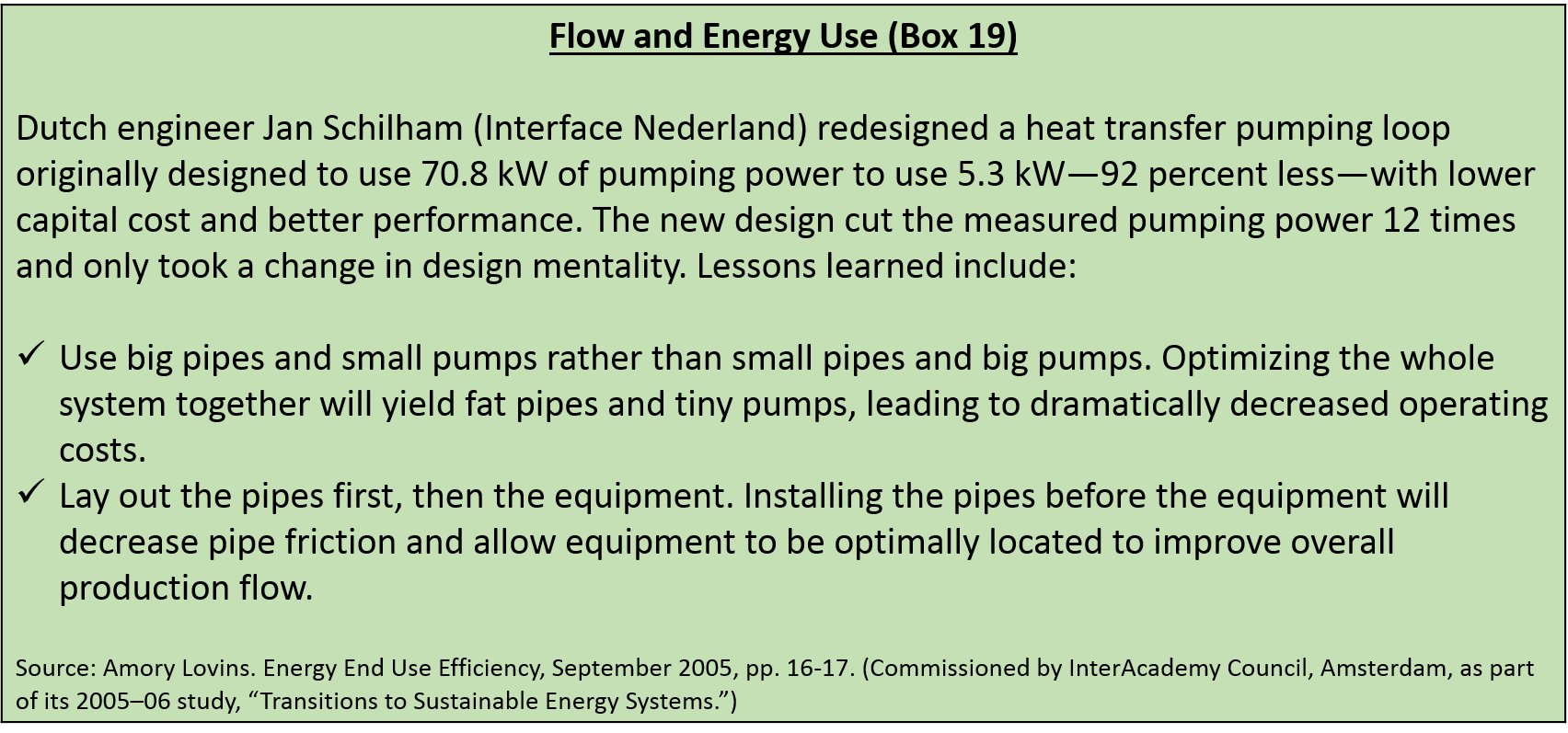
Encourage Energy Efficiency with Standard Work, Visual Controls, Employee Engagement and Mistake-Proofing
Standard Work and Energy Use

Your facility can maximize Lean and energy gains by incorporating energy reduction best practices into standard work (e.g., consider drawing from the Questions for Understanding Energy Use and the Energy Reduction Checklist in Boxes 7 and 16 of this toolkit). Example uses of standard work include:
- Build energy-reduction best practices into training materials, in-house regulations, and standard work for equipment operation and maintenance
- Include energy-reduction tips in weekly team meetings and monthly facility newsletters
- Add energy-reduction best practices into “shine” checklists used when implementing 5S (or 5S+Safety)2
The Pacific Northwest Pollution Prevention Resource Center (PPRC) prepared a Facility Checklist for Identifying Environmental Issues During Lean3. This checklist is intended for use on the manufacturing floor to help companies identify additional environmental opportunities, including, but not limited to, energy efficiency and greenhouse gas emission reduction opportunities. Table 4, below, is an adaptation of the Energy Use portion of the checklist highlighting the things to look for and some of the questions you should ask when assessing your facility.
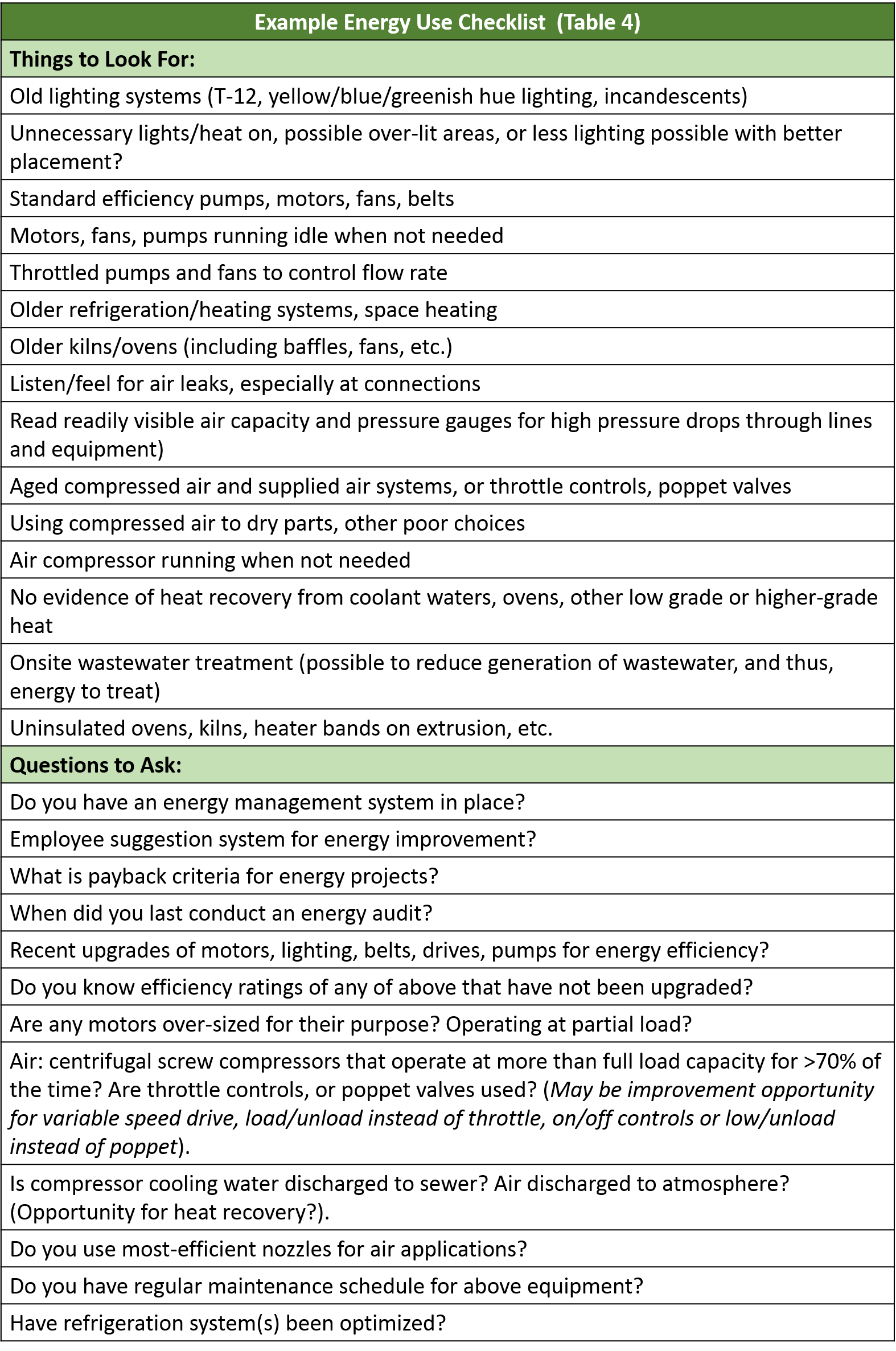
Visual Controls

These easy-to-use cues can be as simple as the following techniques:
- Color-code pipes and other facility conveyances to help operators quickly identify and report key information (e.g., leaks)
- Install a sign over on/off switches or power outlets to remind operators to turn off or unplug equipment that is not in use (for example, see Figure 5)
- Identify the annual energy cost, energy use, and/or carbon emissions of equipment if it is left on continuously and display it on the equipment to raise awareness and encourage conversation.

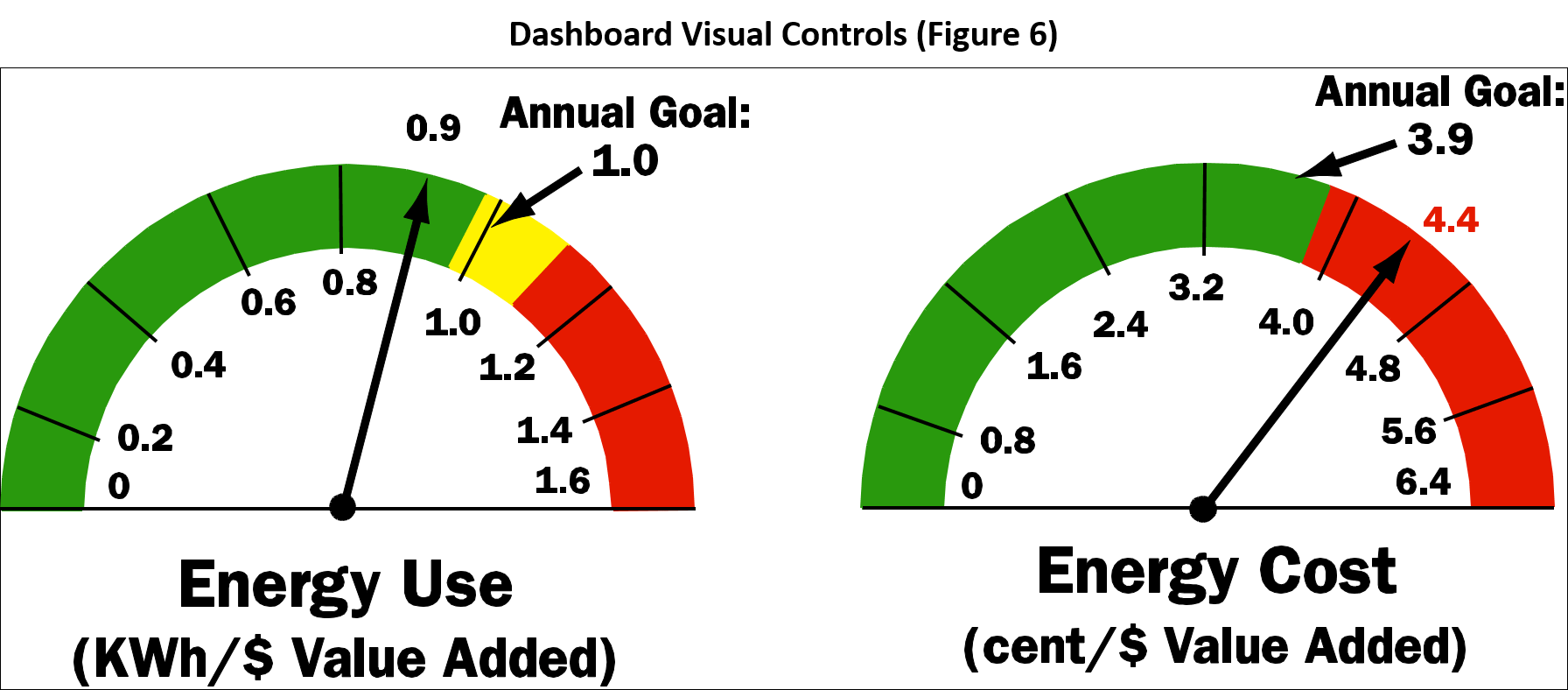
Engaging Employees in Energy & Greenhouse Gas Management Efforts
Employees are one of your strongest assets when implementing your energy and greenhouse gas management programs. Getting them involved through competition, awards, and recognition is a great way to help employees feel like part of these efforts, and if they own the improvements it will be much easier to sustain any changes. There are several ways companies have engaged employees including:
- Competition and Pledges
- Recognition and Rewards
Competition and Pledges
By fostering interest in energy reduction and encouraging employees to take the initiative to reduce their energy consumption, a company can save thousands of dollars each year. Cummins, Inc., an engine manufacturing company in Columbus, Indiana, created a program to encourage employees to keep energy use to a minimum over holiday shutdowns. The 2008 and 2009 “Unplugged Challenge” campaigns saved a combined 1,900 tons of greenhouse gas emissions and $1.2 million4.
Cummins has also piloted an “Energy Champion” program, an intensive weeklong program to empower employees and equip them with the knowledge to implement energy saving practices both at work and at home. Figure 7 shows examples of the materials Cummins developed for this campaign.

Recognition & Rewards
Another way to engage employees is to create recognition programs or other incentives for improving energy use within the company. This is an area where you can get creative. Look at creating a program that recognizes the team or organizational unit who has reduced their energy use the most, or who has had the most inventive solution to an energy or greenhouse gas issue. Post this information in a break room or other prominent common space.
You may also want to consider a monetary award or paid time off to the employee who comes up with a great cost saving idea. Sharing the benefit of these improvements with the employees only makes them want to work harder to identify additional areas where energy and cost savings can be found.
Mistake-Proofing

One simple energy-efficient action is to automatically power down energy-consuming equipment when not in use. Process equipment and lighting do not always need to be on or energized. Mistake-proofing devices such as occupancy sensors and lock-out/tag-out de-energizing steps are a simple, low-cost means to power down equipment that is not in use. By mistake-proofing equipment, a facility can waste less energy, time, and resources, as well as prevent rework.
Reduce Greenhouse Gas Emissions Through Transportation Efficiencies
Transportation in the form of personnel travel, product shipment, and product movement between facilities is often a large contributor to a company’s greenhouse gas emissions. Companies can significantly reduce their greenhouse gas emissions using a variety of tools including employee commuting programs, looking into alternative fuels, and well-planned just-in-time deliveries.
Finding Efficiencies in Vehicle Fleet and Mobile Equipment
In America today, about 28% of the energy we use goes to transporting people and goods from one place to another5. The majority of companies use vehicles and other mobile equipment as an integral part of their daily operations—from maintenance trucks used for parks and recreation to indoor and outdoor forklifts and other gas-powered equipment. These vehicles and equipment burn gasoline, diesel, and other fuels, which results in greenhouse gas emissions. In addition, vehicles with air conditioning or refrigeration equipment use refrigerants that can leak.
Emissions from vehicles and mobile equipment are a great place to look for savings. Several strategies for reducing emissions and maximizing efficiency include:
- Use alternative fuels (including corn or cellulosic ethanol, bio-diesel, natural gas and even diesel, and possibly in the future, hydrogen fuel cells)
- Use hybrid electric vehicles
- Reduce total vehicle miles traveled
- Reduce overall idling time for all vehicles
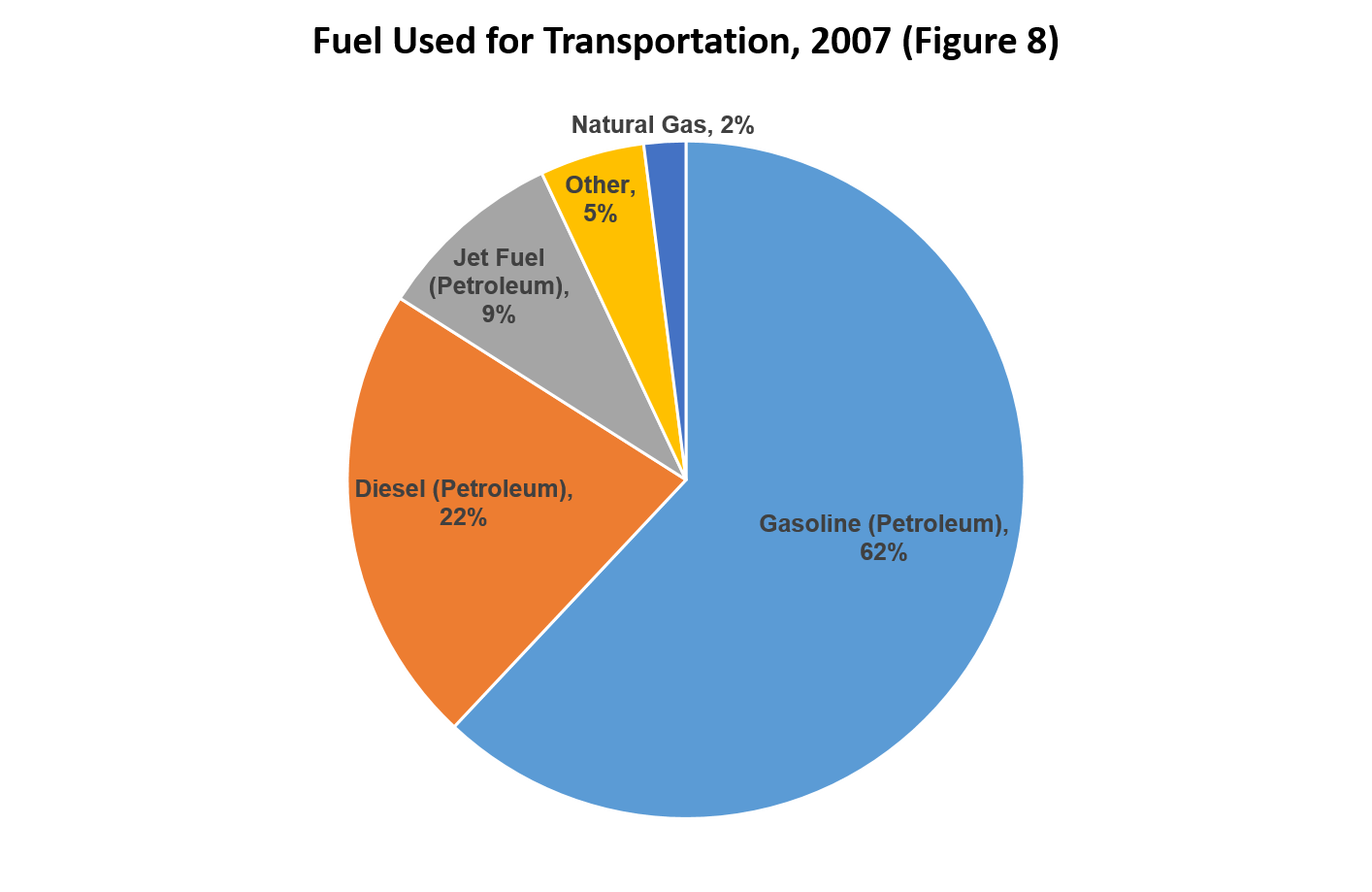

EPA also has a program that can help you reduce emissions from your vehicle fleet. SmartWay is an innovative brand that represents environmentally cleaner, more fuel-efficient transportation options. The SmartWay brand identifies a variety of different products and services related to transportation. Vehicles, fuel options, partnerships, and financing information are available on the website HERE.
These strategies do not just apply to transportation outside of you facility. Consider what changes can be made to the way you transport your materials around your facility. Forklifts can be a major emission source. Using Lean techniques you may be able to optimize the plant layout in such a way that you no longer need forklifts (see section on Plant Layout above). If, however, you just cannot get away from using forklifts, consider purchasing electric models.
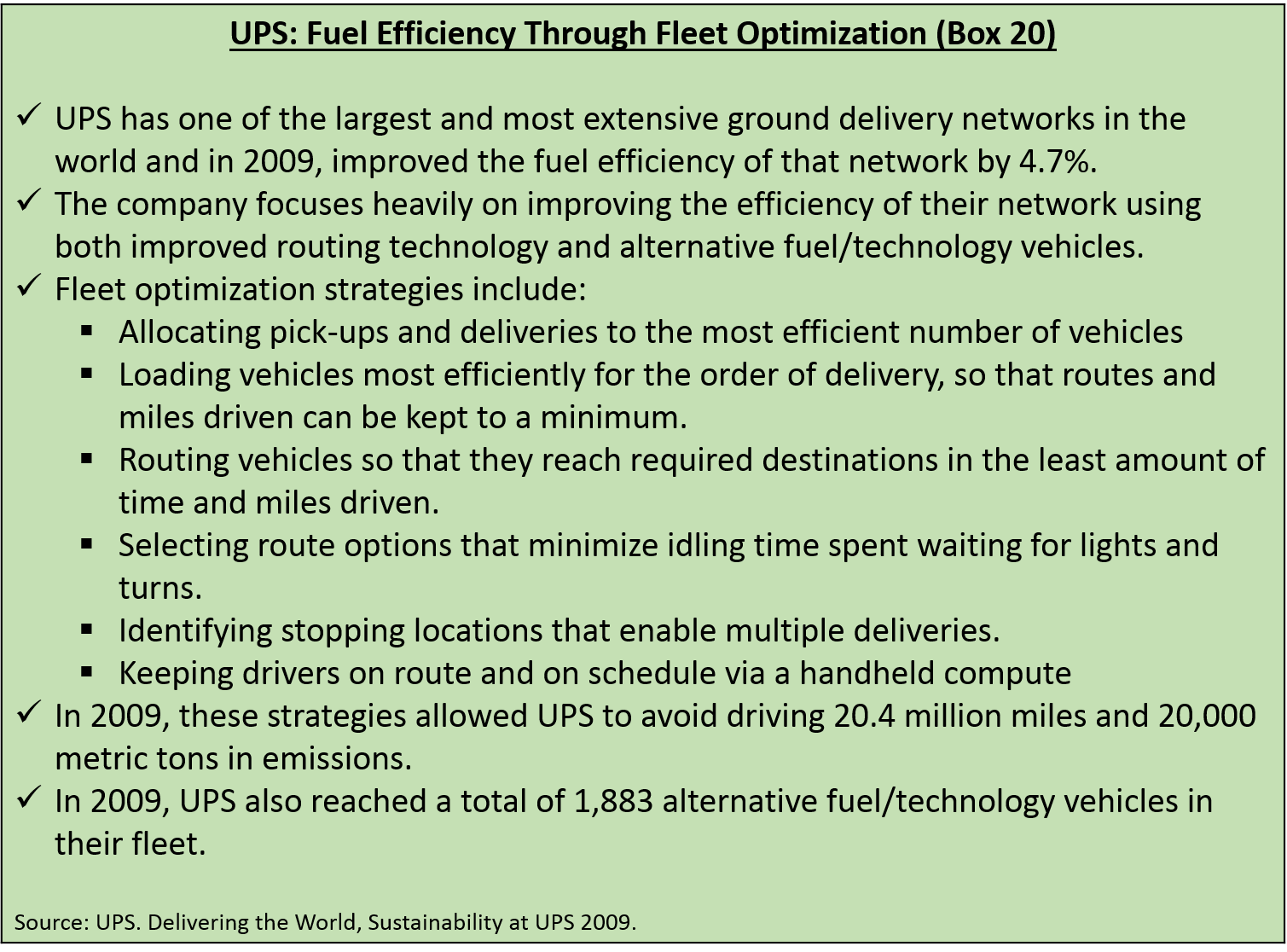

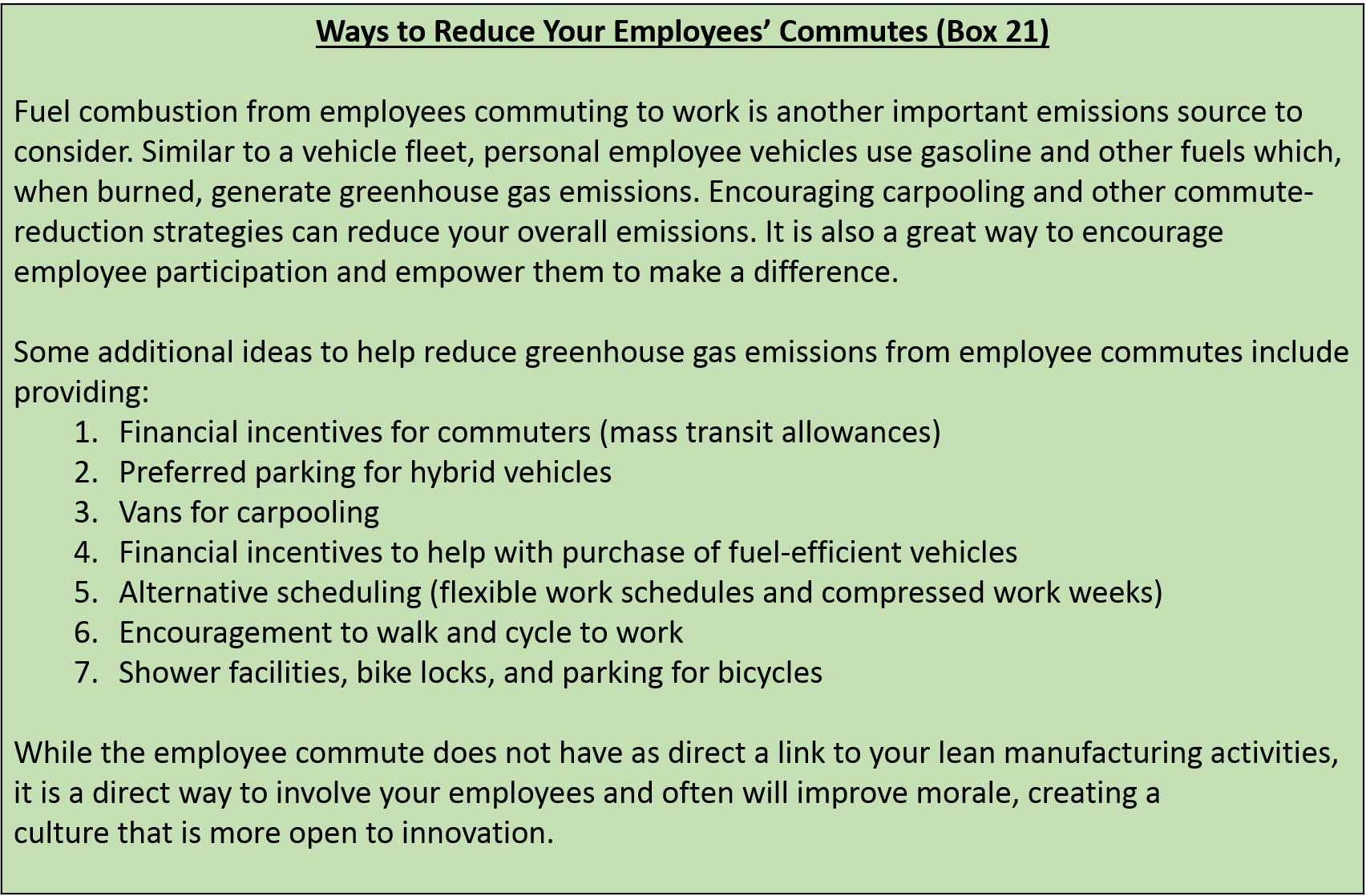
Footnotes
1 Discussion with James Breeze, Energy Engineer/Project Leader, Worldwide Energy Office, Eastman Kodak Company, September 2007.
2 5S is a Lean method involving five steps (Sort, Set in order, Shine, Standardize, and Sustain) to establish a clean, neat, and orderly workplace. Many companies add a sixth “S” for Safety.
3 Pacific Northwest Pollution Prevention Resource Center. Facility Checklist for Identifying Environmental Issues during Lean. March 2009.
4 Cummins, Inc. Sustainability Report 2009-2010.
5Source: U.S. Energy Information Administration, Annual Energy Review 2009.
Toolkit Navigation
- Contents & Acknowledgements
- Executive Summary
- Preface
- Chapter 1: Introduction
- Chapter 2: Integrating Lean, Energy Efficiency and Greenhouse Gas Management
- Chapter 3: Overview of Energy Use and Lean
- Chapter 4: Energy and Greenhouse Gas Assessment Strategies
- Chapter 5: Energy and Greenhouse Gas Emission Reduction Tools and Strategies
- Chapter 6: Conclusion
- Appendix A: Energy and Greenhouse Gas Management Service Providers, Resources and Tools
- Appendix B: Sector-Focused Energy Reduction and Greenhouse Gas Management Resources
- Appendix C: Energy Conversion Resources and Rules of Thumb for Estimating Energy Cost Savings