Lean & Energy Toolkit: Chapter 1
Introduction
- Benefits of Coordinating Lean Energy and Greenhouse Gas Management
- Cost Savings
- Greenhouse Gas and Environmental Risk Management
- Competitive Advantage
- Footnotes
- Toolkit Navigation
Benefits of Coordinating Lean and Energy Management
Energy is a vital (and often costly) input to most production processes and value streams. By thinking explicitly about unnecessary energy use as another “waste,” Lean implementers can significantly reduce costs and enhance competitiveness, while also achieving environmental performance goals.
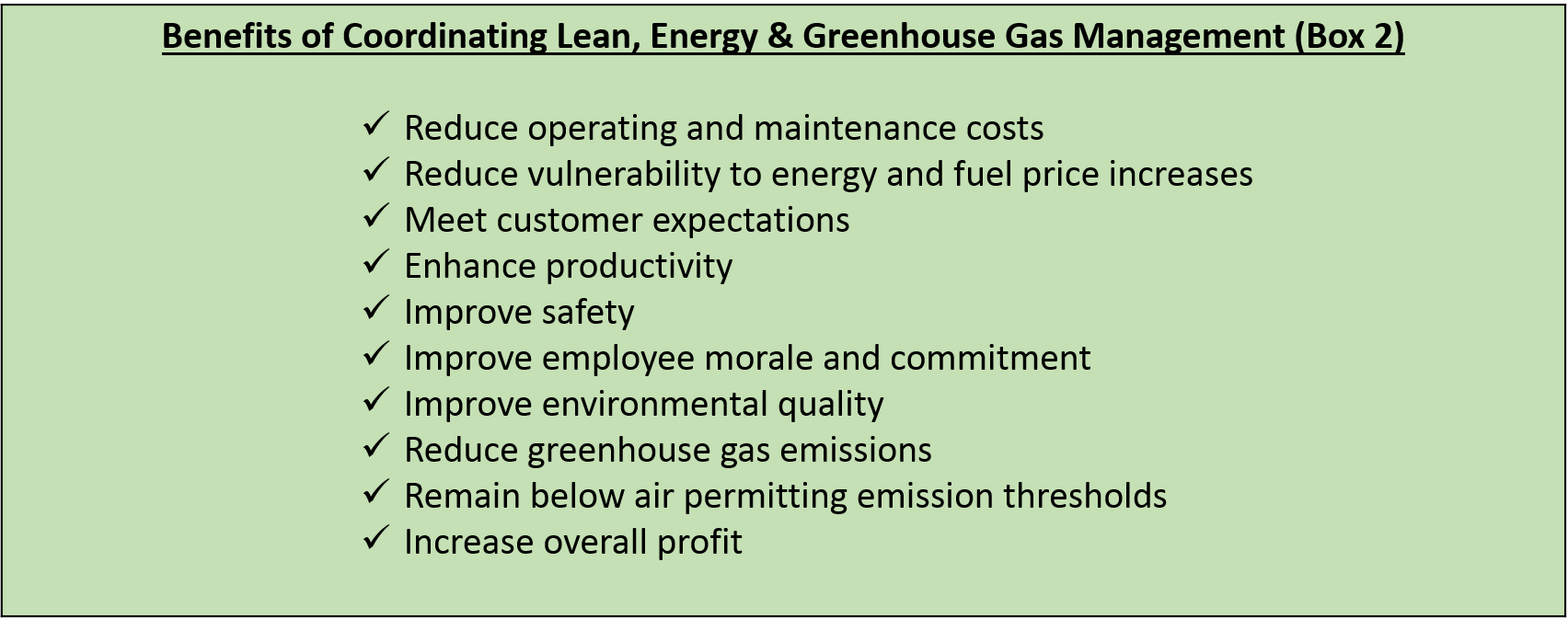
Cost Savings
Energy costs can have a significant impact on the financial performance of businesses. A 2009 survey of corporations conducted by Siemens found that energy cost savings are the top driver for corporate sustainability efforts and seventy-two percent of all respondents reported that lowered operating costs were the reason their firms participated in sustainability initiatives in general1.
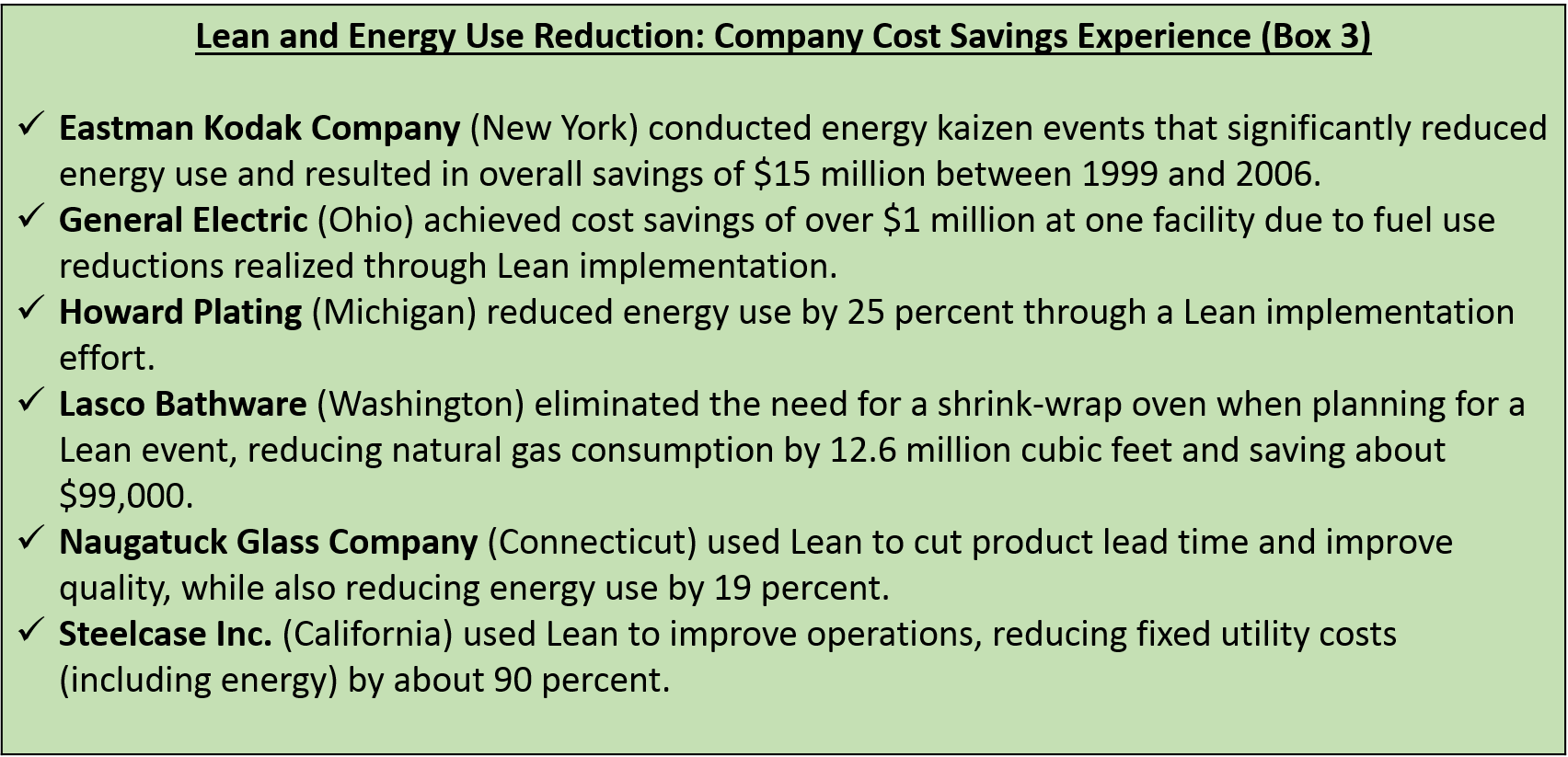

Greenhouse Gas and Environmental Risk Management
The environmental and climate impacts of energy use are a major issue facing industry and society. Carbon dioxide (CO2), a major greenhouse gas, is emitted to the atmosphere directly when fuels are combusted on-site and indirectly when electricity is consumed (particularly when fossil fuels are used to generate the electricity). Emissions also occur when fuel is combusted during transportation of goods to and from facilities and within. Lean methodologies can help companies with an effective way to identify opportunities to improve efficiency and reduce greenhouse gas emissions. This reduces business risks associated with greenhouse gas emissions and contributes to reduction targets.
Carbon dioxide is not the only by-product of energy use. On-site combustion of fuels in boilers, ovens, vehicles, and equipment can emit a variety of regulated pollutants, including carbon monoxide (CO), sulfur dioxide (SO2), nitrogen oxide (NOX), particulate matter (PM), volatile organic compounds (VOCs), and a variety of air toxics.
Combustion pollutant emissions can affect worker health, and trigger the need for costly permitting, monitoring, and emission controls. More broadly, reducing air emissions from combustion activities can help protect neighboring communities and public health. Storage and handling of fuels also pose a variety of worker health, safety, and environmental costs and risks, even in the absence of spills. Lean efforts can directly target and mitigate these impacts and risks.
Competitive Advantage
Identifying and eliminating energy waste through Lean can improve a company’s ability to compete in several ways. First, reducing the energy intensity of production activities and support processes directly lowers recurring operating costs with direct bottom line and competitiveness impacts. When asked by the Economist how the recent economic downturn would affect companies’ approaches to carbon reduction, 47 percent of respondents stated they planned to improve their focus as a cost saving measure2.
Second, eliminating energy waste and the associated environmental impacts through Lean can foster competitive advantage for some businesses. Customers and employees may view proactive environmental improvement efforts as an important attribute, affecting customer loyalty and the ability to attract and retain employees. Participation in climate partnership programs or local climate initiatives can also provide businesses with public recognition for their energy use reduction achievements. For businesses that manufacture appliances, electronics, and other products that consume energy, Lean design methods can be used to lower the lifetime energy use of products.
It is not surprising that most of the major companies that have received awards from the EPA’s ENERGY STAR Program—companies such as 3M, Eastman Kodak, and Toyota—are also leaders in implementing Lean and Six Sigma. Energy waste is clearly on the radar of leading Lean companies. In addition, ENERGY STAR certification for energy-efficient products is an increasingly important factor in consumer-purchase decisions. For more information, visit the ENERGY STAR site.
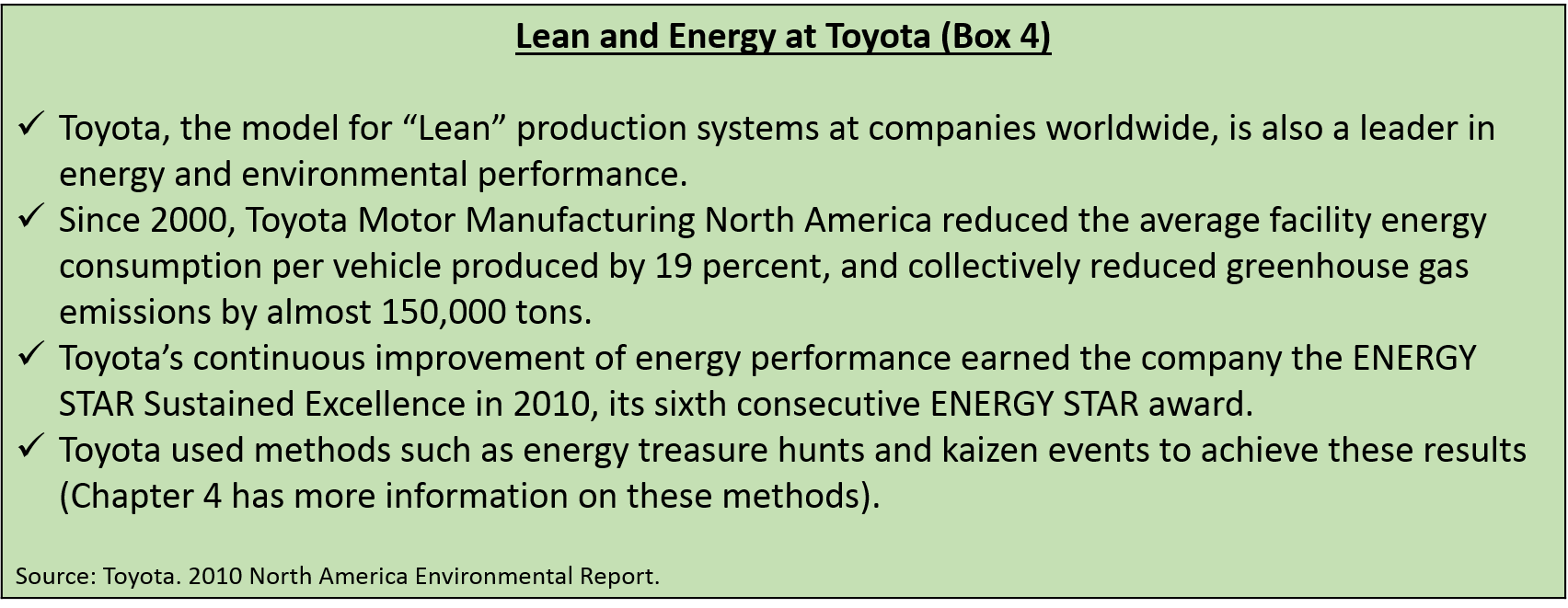
Footnotes
1 Siemens (2009). Greening of Corporate America: The Pathway to Sustainability from Strategy to Action. McGraw-Hill Construction.
2 Economist Intelligence Unit (2009), Countdown to Copenhagen: Government, Business, and the Battle against Climate Change Survey published by The Economist Magazine.
Toolkit Navigation
- Contents & Acknowledgements
- Executive Summary
- Preface
- Chapter 1: Introduction
- Chapter 2: Integrating Lean, Energy Efficiency and Greenhouse Gas Management
- Chapter 3: Overview of Energy Use and Lean
- Chapter 4: Energy and Greenhouse Gas Assessment Strategies
- Chapter 5: Energy and Greenhouse Gas Emission Reduction Tools and Strategies
- Chapter 6: Conclusion
- Appendix A: Energy and Greenhouse Gas Management Service Providers, Resources and Tools
- Appendix B: Sector-Focused Energy Reduction and Greenhouse Gas Management Resources
- Appendix C: Energy Conversion Resources and Rules of Thumb for Estimating Energy Cost Savings